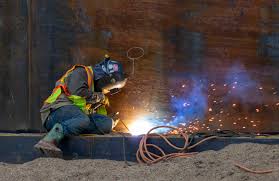
Mastering Tank Weld Fabrication: Ensuring Quality and Safety in Every Joint
Tank Weld Fabrication: Ensuring Quality and Safety
Tank weld fabrication is a crucial process in the production of tanks used in various industries such as oil and gas, chemical, and water treatment. The quality of welds in tanks is essential to ensure structural integrity, prevent leaks, and maintain safety standards.
Welding plays a significant role in tank fabrication, as it joins the different components of a tank together to create a seamless and durable structure. Skilled welders use various welding techniques such as MIG (Metal Inert Gas) welding, TIG (Tungsten Inert Gas) welding, and submerged arc welding to achieve strong and reliable welds.
Quality control is paramount in tank weld fabrication to guarantee the strength and reliability of the welded joints. Inspections are conducted throughout the fabrication process to detect any defects or imperfections that could compromise the integrity of the tank.
Additionally, safety measures are strictly adhered to during tank weld fabrication to protect workers from potential hazards associated with welding activities. Proper ventilation, personal protective equipment (PPE), and adherence to welding procedures are essential to create a safe working environment.
By investing in high-quality materials, skilled welders, rigorous quality control processes, and strict adherence to safety standards, tank weld fabrication ensures that tanks meet industry requirements for performance, durability, and safety.
Overall, tank weld fabrication is a critical aspect of tank production that requires precision, expertise, and attention to detail. By prioritising quality and safety in every step of the fabrication process, manufacturers can deliver tanks that meet the highest standards of excellence.
Essential FAQs on Tank Weld Fabrication: Techniques, Safety, and Standards
- What is tank weld fabrication?
- Why is welding important in tank fabrication?
- What are the common welding techniques used in tank fabrication?
- How is quality control maintained in tank weld fabrication?
- What safety measures are taken during tank weld fabrication?
- What materials are typically used in tank weld fabrication?
- How can defects in welded joints be detected and addressed?
- What standards and regulations govern tank weld fabrication?
What is tank weld fabrication?
Tank weld fabrication refers to the process of welding together the components of a tank to create a unified and structurally sound storage vessel. This essential process involves skilled welders using various welding techniques to join materials such as steel, aluminium, or stainless steel to form a seamless tank structure. The quality and precision of tank weld fabrication are critical factors in ensuring the integrity, durability, and safety of the tank. By meticulously welding the components together and adhering to industry standards for quality control and safety, tank weld fabrication plays a vital role in producing reliable tanks for use in industries such as oil and gas, chemical processing, and water treatment.
Why is welding important in tank fabrication?
Welding plays a crucial role in tank fabrication due to its significance in joining the various components of a tank together. The quality of welds directly impacts the structural integrity, leak resistance, and overall safety of the tank. Skilled welders utilise different welding techniques to create strong and reliable joints that can withstand the demands placed on tanks in industries such as oil and gas, chemical processing, and water treatment. Without high-quality welding processes, tanks would be prone to failure, compromising operational efficiency and posing potential safety risks. Therefore, welding is essential in tank fabrication to ensure that tanks meet stringent industry standards for performance, durability, and safety.
What are the common welding techniques used in tank fabrication?
In tank fabrication, several common welding techniques are utilised to ensure the structural integrity and quality of welded joints. Some of the most frequently used welding techniques include MIG (Metal Inert Gas) welding, TIG (Tungsten Inert Gas) welding, and submerged arc welding. These methods are chosen based on factors such as the type of material being welded, the thickness of the metal components, and the desired strength of the welds. Skilled welders employ these techniques with precision to create durable and reliable tanks that meet industry standards for performance and safety.
How is quality control maintained in tank weld fabrication?
Quality control in tank weld fabrication is maintained through a series of rigorous processes and inspections that ensure the integrity and reliability of welded joints. Skilled welders follow industry standards and best practices to perform welds using various techniques such as MIG, TIG, and submerged arc welding. Throughout the fabrication process, inspections are conducted to identify any defects or imperfections in the welds. These inspections help detect issues early on, allowing for timely corrections and ensuring that the final product meets stringent quality requirements for structural strength and safety. By implementing thorough quality control measures, manufacturers can uphold high standards of excellence in tank weld fabrication.
What safety measures are taken during tank weld fabrication?
Safety measures are of utmost importance during tank weld fabrication to ensure the well-being of workers and the integrity of the final product. Various safety protocols are implemented, including providing proper ventilation to reduce exposure to welding fumes, ensuring the use of personal protective equipment (PPE) such as helmets, gloves, and protective clothing, conducting regular safety inspections to identify and address potential hazards, and adhering to established welding procedures to minimise risks. By prioritising safety measures throughout the tank weld fabrication process, companies can create a secure working environment and produce tanks that meet stringent safety standards.
What materials are typically used in tank weld fabrication?
In tank weld fabrication, a variety of materials are commonly used to meet the specific requirements of different industries and applications. Carbon steel is a popular choice for its strength and affordability, making it suitable for a wide range of tank types. Stainless steel is preferred for its corrosion resistance, making it ideal for tanks that store corrosive substances. Aluminium is often used for lightweight tanks or those requiring high conductivity. Additionally, materials such as nickel alloys and titanium may be employed for tanks operating in extreme conditions or requiring exceptional durability. The selection of materials in tank weld fabrication plays a crucial role in ensuring the longevity, performance, and safety of the tanks produced.
How can defects in welded joints be detected and addressed?
Detecting and addressing defects in welded joints is a crucial aspect of ensuring the quality and integrity of tank weld fabrication. Various non-destructive testing methods, such as ultrasonic testing, radiographic testing, magnetic particle testing, and dye penetrant inspection, are employed to identify any imperfections or discontinuities in the welded joints. Once defects are detected, skilled inspectors can determine the severity of the issue and recommend appropriate corrective actions, such as re-welding or grinding out the defect. By promptly addressing defects in welded joints through thorough inspection and remediation processes, manufacturers can uphold high standards of quality and safety in tank weld fabrication.
What standards and regulations govern tank weld fabrication?
In tank weld fabrication, adherence to specific standards and regulations is paramount to ensure the quality, safety, and integrity of the tanks produced. Various standards such as BS EN 14015, API 650, and ASME Boiler and Pressure Vessel Code govern different aspects of tank design, materials, fabrication processes, and inspection requirements. These standards outline the minimum requirements for welding procedures, qualifications of welders, material selection, non-destructive testing methods, and quality control measures to be followed during tank weld fabrication. By complying with these established standards and regulations, manufacturers can guarantee that their tanks meet industry best practices and regulatory requirements for optimal performance and safety.