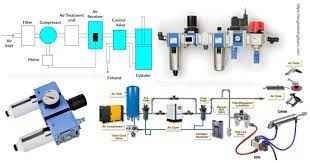
Maximizing Efficiency: The Key to Successful Pneumatic Systems Installation
Pneumatic Systems Installation: Enhancing Efficiency and Performance
In today’s industrial landscape, efficiency and performance are key factors that can make or break a business. One technology that has proven to be highly effective in achieving these goals is the use of pneumatic systems. These systems, powered by compressed air, offer a range of benefits that make them an ideal choice for various applications.
Pneumatic systems are widely used in industries such as manufacturing, automotive, food processing, and packaging. They provide a reliable and cost-effective solution for automating processes, powering machinery, and controlling equipment. From simple tasks like operating valves and cylinders to complex operations involving conveyor systems and robotic arms, pneumatic systems have become an integral part of modern industrial setups.
Installing a pneumatic system requires careful planning and expertise. It involves selecting the right components, designing the layout, ensuring proper air supply, and integrating it seamlessly with existing machinery or infrastructure. This is where professional pneumatic system installation services come into play.
By engaging experienced installers who specialize in pneumatic systems, businesses can ensure a smooth and efficient installation process. These experts possess in-depth knowledge of the different components involved – compressors, air filters, regulators, valves, actuators – and understand how they work together to create a reliable system.
During the installation process, attention to detail is crucial. Properly sizing pipes and fittings to minimize pressure drops and leaks is essential for maintaining optimal system performance. Additionally, ensuring proper filtration of compressed air is vital to prevent contamination that could damage sensitive components or compromise product quality in industries such as pharmaceuticals or electronics manufacturing.
Moreover, professional installers can assist with system optimization by fine-tuning pressure settings and flow rates according to specific requirements. This ensures that the system operates at its highest efficiency while minimizing energy consumption.
Safety is another critical aspect of pneumatic system installation. Professionals adhere to strict safety guidelines during each step of the process to prevent accidents, leaks, or malfunctions that could pose risks to personnel or equipment. They also conduct thorough testing and inspections to verify the integrity of the system before it goes into operation.
Once a pneumatic system is installed, businesses can benefit from increased productivity, reduced downtime, and improved overall efficiency. These systems offer fast response times, precise control, and high power-to-weight ratios. They are also known for their durability and low maintenance requirements, making them a cost-effective choice in the long run.
In conclusion, pneumatic systems have become indispensable in modern industries seeking enhanced efficiency and performance. Professional installation services ensure that these systems are seamlessly integrated into existing setups while optimizing their operation. By investing in proper installation from experts who understand the intricacies of pneumatic systems, businesses can unlock the full potential of this technology and gain a competitive edge in their respective fields.
9 Pros of Pneumatic Systems Installation: Advantages, Benefits, and Features
- Quick and easy installation – Pneumatic systems are relatively fast and easy to install, as no wiring or complex programming is required.
- Low maintenance requirements – Once installed, pneumatic systems require very little maintenance. This makes them a cost-effective solution for many applications.
- Reduced risk of electrical hazards – Unlike electrical systems, pneumatic systems do not pose any risks of electric shock or fire hazards. This makes them a safer option in certain environments.
- Increased accuracy and precision – Pneumatic systems can be programmed to operate with extreme accuracy and precision due to their consistent nature and lack of variability in pressure levels over time.
- Greater energy efficiency – Compared to traditional mechanical solutions, pneumatic systems use less energy while providing greater control over the process they are used for, resulting in increased efficiency overall.
- Improved reliability – Pneumatic components have fewer moving parts than traditional mechanical components, making them more reliable over time due to fewer potential points of failure or wear-and-tear issues that can occur with mechanical components over time..
- Cost effective – The cost of installing a pneumatic system is often much lower than other automated solutions such as robotics or hydraulics due to the low cost of components and ease of installation
- Versatile – Pneumatic systems can be used for a variety of different tasks ranging from simple on/off operations all the way up to complex robotic movements depending on the complexity of the system installed
- Flexible – With its ability to be easily modified and adjusted based on changing needs, a pneumatic system provides an incredibly flexible solution that can adapt quickly when changes need to be made
Drawbacks of Pneumatic System Installation in the UK: A Comprehensive Overview
- Expensive to install – Pneumatic systems require a lot of equipment and components, which can be expensive to purchase and install.
- High maintenance costs – Pneumatic systems require regular maintenance to ensure they are running correctly and efficiently, which can be costly.
- Complex installation process – Installing pneumatic systems can be complex due to the various components that need to be connected together and configured correctly in order for it to work properly.
- Limited scalability – Once installed, it is often difficult or impossible to scale up the system as your needs change over time without having to replace parts or make significant changes in the configuration of the system.
- Limited flexibility – Pneumatic systems are not as flexible as other types of automation systems, meaning that they may not be suitable for applications where frequent changes in the production process are required.
- Noise pollution – The operation of pneumatic systems can generate a considerable amount of noise which may disturb people living or working nearby if not adequately soundproofed
Quick and easy installation – Pneumatic systems are relatively fast and easy to install, as no wiring or complex programming is required.
Quick and Easy Installation: The Advantage of Pneumatic Systems
When it comes to installing new systems or upgrading existing ones, time is often a critical factor. In this regard, pneumatic systems offer a significant advantage – they are quick and easy to install. Unlike other technologies that require extensive wiring or complex programming, pneumatic systems simplify the installation process, saving both time and effort.
One of the reasons for the ease of installation is that pneumatic systems rely on compressed air as their power source. This eliminates the need for intricate electrical wiring, reducing the complexity of the installation process. Without the requirement for extensive cabling, businesses can save valuable time and resources during system setup.
Additionally, pneumatic systems do not require complex programming or software configuration. Instead, they operate using simple mechanical components such as valves and actuators that respond directly to changes in air pressure. This straightforward design makes it easier for installers to integrate pneumatic systems into existing setups without extensive programming knowledge or specialized training.
The absence of complicated wiring and programming also means that troubleshooting and maintenance become more straightforward tasks. In case of any issues or component failures, identifying and replacing the faulty part is generally easier compared to intricate electronic systems. This ease of maintenance ensures minimal downtime and allows businesses to quickly resume their operations.
The quick and easy installation process associated with pneumatic systems offers several advantages for businesses. Firstly, it reduces overall project costs by minimizing labor hours required for installation. Secondly, it allows for faster system implementation, enabling businesses to start reaping the benefits sooner rather than later.
Moreover, this simplicity in installation also provides flexibility when it comes to system modifications or expansions in the future. Adding new components or making adjustments to accommodate changing needs can be accomplished more efficiently with pneumatic systems compared to complex electronic alternatives.
In conclusion, one of the significant advantages of pneumatic system installation is its quick and easy nature. By eliminating complex wiring requirements and intricate programming, businesses can save time, reduce costs, and enjoy a hassle-free installation process. Whether it’s for new systems or upgrades, pneumatic systems offer a straightforward solution that allows companies to enhance their operations swiftly and efficiently.
Low maintenance requirements – Once installed, pneumatic systems require very little maintenance. This makes them a cost-effective solution for many applications.
Low Maintenance Requirements: A Cost-Effective Advantage of Pneumatic Systems Installation
When it comes to choosing a system for industrial applications, maintenance costs can significantly impact the overall budget. That’s where pneumatic systems shine, offering a distinct advantage with their low maintenance requirements.
Once a pneumatic system is installed and properly set up, it operates reliably with minimal upkeep. This makes it an attractive and cost-effective solution for various industries, including manufacturing, packaging, and automation.
One of the primary reasons for the low maintenance needs of pneumatic systems is their simplicity. These systems consist of basic components such as compressors, valves, cylinders, and tubing. Unlike complex electrical or hydraulic systems, pneumatic systems have fewer moving parts that can wear out or require frequent servicing.
Additionally, the use of compressed air as the power source eliminates the need for regular lubrication or fluid changes. This further reduces maintenance tasks and associated costs. The absence of lubricants also means less risk of contamination in sensitive industries like food processing or electronics manufacturing.
Moreover, pneumatic systems are designed to withstand harsh environments and demanding operating conditions. They are resistant to dust, dirt, humidity, and extreme temperatures. This durability ensures that they can withstand rigorous use without compromising performance or requiring frequent repairs.
Another advantage of low maintenance requirements is the reduction in downtime. With fewer breakdowns and servicing needs, businesses can maximize productivity and minimize costly interruptions in their operations. This leads to increased efficiency and improved profitability in the long run.
However, while pneumatic systems do require less maintenance compared to other alternatives, it’s important not to overlook routine checks and inspections. Regular visual inspections can help identify any potential issues before they escalate into major problems. Checking for leaks, ensuring proper air pressure levels, and inspecting valves or seals are simple tasks that can be performed periodically to maintain optimal system performance.
In conclusion, one of the most significant advantages of pneumatic systems installation is their low maintenance requirements. These systems operate reliably with minimal upkeep, making them a cost-effective choice for businesses in various industries. By minimizing maintenance tasks and reducing downtime, pneumatic systems contribute to improved efficiency, productivity, and ultimately, the bottom line.
Reduced risk of electrical hazards – Unlike electrical systems, pneumatic systems do not pose any risks of electric shock or fire hazards. This makes them a safer option in certain environments.
Reduced Risk of Electrical Hazards: The Safety Advantage of Pneumatic Systems
When it comes to ensuring a safe working environment, businesses must prioritize the mitigation of potential hazards. One significant advantage of pneumatic systems installation is the reduced risk of electrical hazards, making them a safer option in certain environments.
Unlike electrical systems that rely on the flow of electricity to power machinery and equipment, pneumatic systems utilize compressed air as their source of energy. This fundamental difference eliminates the risks associated with electric shock or fire hazards that can occur with electrical systems.
In environments where moisture, dust, or flammable substances are present, such as manufacturing plants or chemical facilities, the use of electrical equipment can pose a significant safety concern. Even with proper insulation and grounding measures in place, there is always a possibility of electrical malfunctions leading to shocks or sparks that could ignite flammable materials.
Pneumatic systems offer an alternative solution in such situations. By utilizing compressed air instead of electricity, these systems eliminate the risk of electric shock entirely. This factor alone significantly enhances safety for workers operating or maintaining machinery within these environments.
Furthermore, pneumatic systems are not susceptible to short circuits or power surges that can potentially lead to fires. Electrical malfunctions caused by damaged wiring, overloaded circuits, or faulty components can have devastating consequences in high-risk settings. By opting for pneumatic systems installation instead, businesses can effectively mitigate these fire hazards and ensure a safer working environment for their employees.
Additionally, pneumatic systems often require less maintenance than their electrical counterparts. Without complex wiring and delicate electronic components susceptible to wear and tear or environmental factors, pneumatic systems tend to be more robust and durable. This reduces the need for frequent inspections and repairs associated with electrical systems, further minimizing potential risks.
It is important to note that while pneumatic systems offer significant safety advantages over electrical systems in certain environments, they are not without their own set of considerations. Proper installation, regular maintenance, and adherence to safety guidelines are still essential to ensure the optimal performance and safety of pneumatic systems.
In conclusion, the reduced risk of electrical hazards is a notable advantage of pneumatic systems installation. By eliminating the potential for electric shock and fire hazards, these systems provide a safer option in environments where moisture, dust, or flammable substances are present. Businesses can prioritize the well-being of their employees and safeguard against potential accidents by opting for pneumatic systems that offer a reliable and safe alternative to electrical power.
Increased accuracy and precision – Pneumatic systems can be programmed to operate with extreme accuracy and precision due to their consistent nature and lack of variability in pressure levels over time.
Increased Accuracy and Precision: Unleashing the Potential of Pneumatic Systems
In the world of industrial automation, accuracy and precision are vital for achieving optimal results. Pneumatic systems have emerged as a game-changer in this regard, offering unparalleled levels of accuracy and precision that can greatly enhance productivity and quality.
One of the key advantages of pneumatic systems is their consistent nature. Unlike other power sources that may fluctuate in performance, pneumatic systems operate with a remarkable level of consistency. This consistency is owed to their reliance on compressed air as the driving force. The pressure levels in pneumatic systems remain stable over time, ensuring a reliable and predictable operation.
This inherent consistency makes pneumatic systems an ideal choice for applications that require precise control. By programming these systems, businesses can achieve exceptional accuracy in tasks such as positioning, sorting, and assembly. Whether it’s controlling robotic arms or operating delicate machinery, pneumatic systems can be fine-tuned to perform with extreme precision.
The lack of variability in pressure levels also eliminates the need for constant adjustments or recalibrations. Once properly set up and programmed, pneumatic systems can maintain their accuracy consistently over extended periods without compromising performance. This saves valuable time and resources that would otherwise be spent on frequent calibrations or adjustments.
Moreover, the fast response times offered by pneumatic systems contribute to their enhanced accuracy. These systems can swiftly react to input signals, allowing for precise control even in dynamic environments. Whether it’s rapid actuation of valves or quick adjustments in pressure levels, pneumatic systems excel at delivering instantaneous responses.
The increased accuracy and precision offered by pneumatic systems have far-reaching benefits across various industries. In manufacturing processes where precise measurements are crucial for product quality, such as automotive assembly or electronics production, these systems ensure consistent results that meet stringent standards.
Furthermore, industries that rely on intricate movements or delicate handling tasks benefit greatly from the precise control provided by pneumatic systems. From pick-and-place operations in packaging to intricate assembly tasks in medical device manufacturing, the accuracy and precision of pneumatic systems contribute to improved efficiency and reduced error rates.
In conclusion, the increased accuracy and precision of pneumatic systems have revolutionized industrial automation. Their consistent nature and lack of variability in pressure levels enable businesses to program these systems for precise control, resulting in enhanced productivity, improved quality, and reduced errors. By harnessing the power of pneumatic systems, businesses can unlock new levels of accuracy and precision that lead to success in today’s competitive marketplace.
Greater energy efficiency – Compared to traditional mechanical solutions, pneumatic systems use less energy while providing greater control over the process they are used for, resulting in increased efficiency overall.
Greater Energy Efficiency: The Advantage of Pneumatic Systems Installation
In today’s world, energy efficiency is a top priority for businesses across industries. Finding ways to reduce energy consumption without compromising productivity is a constant challenge. This is where pneumatic systems installation shines, offering a pro that sets it apart from traditional mechanical solutions.
One significant advantage of pneumatic systems is their ability to provide greater energy efficiency. Compared to their mechanical counterparts, pneumatic systems use less energy while still delivering precise control over the processes they are employed for. This results in increased overall efficiency and cost savings for businesses.
Pneumatic systems operate by harnessing compressed air to power various components such as valves, cylinders, and actuators. This method eliminates the need for complex mechanical linkages or electrical motors, which often consume more energy. By relying on compressed air, pneumatic systems can achieve the same level of performance while using less power.
The use of compressed air allows for easy adjustment of pressure and flow rates, providing precise control over the system’s operation. This level of control ensures that only the necessary amount of energy is used at any given time, eliminating wastage and optimizing efficiency.
Moreover, pneumatic systems have quick response times and can be easily turned on or off as needed. Unlike mechanical systems that may require ramp-up or cool-down periods, pneumatic systems offer instant start-up and shut-off capabilities. This further contributes to energy savings by minimizing idle time and reducing overall power consumption.
The simplicity of pneumatic systems also plays a role in their energy efficiency. With fewer moving parts compared to mechanical solutions, there are fewer frictional losses and less wear and tear on components. This translates into reduced maintenance requirements and longer equipment lifespan.
Businesses that invest in pneumatic system installation can enjoy significant benefits beyond just energy savings. Increased efficiency means improved productivity, reduced downtime, and enhanced overall performance. These advantages contribute to cost savings in the long run, making pneumatic systems a smart investment for businesses looking to improve their bottom line.
In conclusion, the greater energy efficiency offered by pneumatic systems installation sets it apart from traditional mechanical solutions. By utilizing compressed air and providing precise control over processes, these systems consume less energy while still delivering optimal performance. Businesses that embrace pneumatic systems can enjoy cost savings, increased productivity, and a greener approach to their operations.
Improved reliability – Pneumatic components have fewer moving parts than traditional mechanical components, making them more reliable over time due to fewer potential points of failure or wear-and-tear issues that can occur with mechanical components over time..
Improved Reliability: The Advantage of Pneumatic Systems Installation
When it comes to industrial applications, reliability is paramount. Businesses rely on their machinery and equipment to operate smoothly and consistently, avoiding costly downtime and delays. This is where pneumatic systems installation shines, offering improved reliability compared to traditional mechanical components.
One of the key reasons for the enhanced reliability of pneumatic systems is their design. Pneumatic components have fewer moving parts compared to their mechanical counterparts. This simplicity translates into a reduced risk of failure or wear-and-tear issues that can occur over time with mechanical components.
With fewer moving parts, there are fewer potential points of failure in a pneumatic system. This means that businesses can enjoy increased uptime and productivity as the chances of unexpected breakdowns or malfunctions are significantly reduced. The streamlined design also simplifies maintenance requirements, making it easier to keep the system in optimal working condition.
Additionally, pneumatic systems are less susceptible to wear-and-tear issues. Mechanical components often experience friction and physical contact between moving parts, leading to eventual degradation and performance decline. In contrast, pneumatic systems operate using compressed air, which eliminates many of these wear-inducing factors.
The absence of direct physical contact between components in a pneumatic system means that there is less chance for parts to degrade or break down due to friction or surface damage. This characteristic allows businesses to benefit from longer service life and increased overall system reliability.
Moreover, the use of compressed air in pneumatic systems provides inherent shock-absorbing capabilities. Mechanical systems may be vulnerable to damage caused by sudden impacts or vibrations during operation. Pneumatic systems, on the other hand, can better withstand such shocks due to the compressibility and cushioning effect of air.
The improved reliability offered by pneumatic systems installation brings numerous advantages for businesses across various industries. It ensures consistent performance over time without compromising efficiency or productivity. With fewer potential points of failure and reduced wear-and-tear, businesses can rely on their pneumatic systems to deliver reliable operation, minimizing costly downtime and maintenance expenses.
In conclusion, the streamlined design and reduced moving parts of pneumatic components make pneumatic systems installation a highly reliable choice for industrial applications. By opting for pneumatics, businesses can enjoy increased uptime, longer service life, and a decreased risk of unexpected breakdowns. The improved reliability of pneumatic systems ultimately translates into enhanced productivity and peace of mind for businesses relying on efficient and dependable machinery.
Cost effective – The cost of installing a pneumatic system is often much lower than other automated solutions such as robotics or hydraulics due to the low cost of components and ease of installation
Cost Effective: The Advantage of Pneumatic Systems Installation
When it comes to automating processes and powering machinery, businesses often face the challenge of finding a solution that balances efficiency with affordability. This is where pneumatic systems installation shines, offering a cost-effective alternative to other automated solutions such as robotics or hydraulics.
One of the primary reasons why pneumatic systems installation is cost effective is the relatively low cost of components. Unlike complex robotic systems or hydraulic setups that require expensive motors, pumps, and intricate control mechanisms, pneumatic systems rely on compressed air as their power source. This means that the components needed for a pneumatic system – such as valves, cylinders, and actuators – are generally more affordable. This affordability extends to maintenance and repairs as well, as pneumatic components are often easier to replace or repair compared to their hydraulic or electronic counterparts.
Furthermore, the ease of installation contributes significantly to the cost-effectiveness of pneumatic systems. The simplicity of these systems allows for faster and more straightforward installation processes compared to more complex alternatives. With fewer intricate parts and wiring requirements, professional installers can complete the setup efficiently, reducing labor costs and minimizing downtime during implementation.
The lower initial investment required for a pneumatic system installation can be particularly advantageous for small and medium-sized businesses with limited budgets. It allows them to automate their processes without breaking the bank or compromising on quality. Additionally, the affordability factor makes it easier for businesses to scale up their operations by adding more pneumatic components or expanding their existing system.
Despite being cost effective, pneumatic systems do not compromise on performance. They offer fast response times, precise control over movements and forces, and high power-to-weight ratios that make them suitable for a wide range of applications across various industries.
In conclusion, when considering automated solutions for powering machinery or automating processes, businesses should not overlook the cost-effective advantages offered by pneumatic systems installation. With lower component costs and ease of installation, these systems provide an affordable option without compromising on performance. By opting for pneumatic systems, businesses can achieve efficiency and productivity gains while keeping their budgets in check.
Versatile – Pneumatic systems can be used for a variety of different tasks ranging from simple on/off operations all the way up to complex robotic movements depending on the complexity of the system installed
Versatile Pneumatic Systems: From Simple Operations to Complex Robotic Movements
When it comes to industrial automation, versatility is a highly desirable trait. This is where pneumatic systems truly shine. With their ability to adapt to a wide range of tasks, pneumatic systems offer businesses the flexibility they need to tackle various operations efficiently.
One of the key advantages of pneumatic systems installation is their versatility. These systems can be tailored to suit different requirements, from simple on/off operations to complex robotic movements. The level of complexity depends on the specific system installed and the components integrated into it.
For simpler tasks, such as operating valves or cylinders, pneumatic systems provide a reliable and cost-effective solution. By harnessing compressed air, these systems can swiftly and precisely control the movement of various mechanical components. This makes them ideal for applications where speed and accuracy are essential.
However, pneumatic systems go beyond basic operations. They have the capability to handle more intricate tasks involving complex robotic movements. By integrating advanced components like servo valves and actuators, these systems can achieve precise positioning, speed control, and synchronized motion for sophisticated automation processes.
This versatility makes pneumatic systems suitable for a wide range of industries. In manufacturing plants, they can be used for material handling, assembly line automation, and packaging processes. In automotive production facilities, they enable precise control over robotic arms for welding or painting tasks. Even in medical settings or laboratories, pneumatic systems find applications in delicate operations that require controlled movements with minimal risk of contamination.
The adaptability of pneumatic systems also extends to their scalability. Whether businesses require a small-scale setup or an extensive network of interconnected components, these systems can be designed and installed accordingly. This scalability allows companies to start with a basic system and gradually expand it as their needs evolve or production volumes increase.
Moreover, the modularity of pneumatic components enables easy integration with existing machinery or infrastructure. This means that businesses can leverage the benefits of pneumatic systems without having to overhaul their entire setup. By incorporating pneumatic technology into their operations, companies can enhance productivity, improve efficiency, and reduce downtime.
In conclusion, the versatility of pneumatic systems is a significant pro when it comes to installation. Their ability to handle a wide range of tasks, from simple on/off operations to complex robotic movements, makes them an invaluable tool for various industries. With the right components and expert installation, businesses can harness the power of pneumatic systems to streamline their processes and achieve optimal performance.
Flexible – With its ability to be easily modified and adjusted based on changing needs, a pneumatic system provides an incredibly flexible solution that can adapt quickly when changes need to be made
Pneumatic Systems Installation: The Power of Flexibility
In today’s fast-paced business environment, adaptability is a crucial trait for success. This is where the flexibility of pneumatic systems truly shines. With their ability to be easily modified and adjusted based on changing needs, pneumatic systems provide an incredibly flexible solution that can adapt quickly when changes need to be made.
One of the key advantages of pneumatic systems installation is their inherent flexibility. These systems are designed to accommodate modifications and adjustments without requiring extensive reconfigurations or costly upgrades. Whether it’s adding new components, changing the layout, or expanding the system’s capabilities, pneumatic systems can be easily adapted to meet evolving requirements.
The modular nature of pneumatic components allows for seamless integration and interchangeability. This means that adding or removing components can be done swiftly and efficiently, enabling businesses to respond promptly to changing production demands or process improvements. This flexibility ensures that downtime is minimized and productivity remains high during system modifications.
Furthermore, pneumatic systems offer a wide range of control options that allow for precise adjustments based on specific needs. By simply adjusting pressure settings or flow rates, operators can fine-tune the system’s performance without major overhauls. This level of control ensures that processes can be optimized for efficiency and productivity.
The ease with which pneumatic systems can be modified also extends to their compatibility with other equipment or machinery. They can seamlessly integrate with existing setups, making it simple to incorporate new tools or devices into the system as needed. This versatility enables businesses to leverage their current infrastructure while still being able to adapt and expand their operations without significant disruptions.
The flexibility provided by pneumatic systems installation has far-reaching benefits across various industries. For example, in manufacturing environments where production requirements may fluctuate frequently, being able to quickly reconfigure a system allows for efficient scaling up or down as needed. In assembly lines where different products are manufactured at different times, the ability to adjust the system’s parameters ensures smooth transitions between product variations.
Moreover, the adaptability of pneumatic systems also contributes to cost-effectiveness. Instead of investing in entirely new systems when changes are required, businesses can modify their existing pneumatic systems, saving both time and money. This flexibility helps maximize the return on investment and provides a sustainable solution for long-term operational needs.
In conclusion, pneumatic systems installation offers a powerful advantage – flexibility. The ability to easily modify and adjust these systems based on changing needs ensures that businesses can adapt quickly and efficiently. From accommodating new components to optimizing performance, pneumatic systems provide a flexible solution that empowers businesses to stay ahead in today’s dynamic market.
Expensive to install – Pneumatic systems require a lot of equipment and components, which can be expensive to purchase and install.
Expensive to Install: The Cost Consideration of Pneumatic Systems Installation
While pneumatic systems offer numerous benefits, it is important to acknowledge that there are some challenges associated with their installation. One significant drawback is the cost involved in purchasing and installing the necessary equipment and components.
Pneumatic systems require a range of specialized components, including compressors, air filters, regulators, valves, and actuators. These components can be quite expensive, especially when considering the quantity needed for a comprehensive system installation. Additionally, the cost of accessories such as pipes, fittings, and connectors must also be taken into account.
Furthermore, the installation process itself can be labor-intensive and time-consuming. Professional expertise is often required to ensure proper integration with existing machinery or infrastructure. This adds to the overall cost of installation as businesses may need to engage experienced installers who specialize in pneumatic systems.
However, it’s important to note that while the initial investment may seem high, pneumatic systems can offer long-term benefits that outweigh the upfront costs. These systems are known for their durability and low maintenance requirements. Once installed correctly, they can provide reliable operation for an extended period without significant ongoing expenses.
It is also worth considering that pneumatic systems offer energy efficiency advantages compared to other alternatives. Their power-to-weight ratio is high, making them suitable for various applications where precise control and fast response times are essential. By optimizing system design and pressure settings during installation, businesses can minimize energy consumption and reduce operational costs in the long run.
To mitigate the financial impact of pneumatic system installation costs, businesses should carefully evaluate their specific needs before making any purchasing decisions. Consulting with experts in this field can help determine an appropriate system size and configuration that aligns with both budgetary constraints and operational requirements.
In conclusion, while it is true that pneumatic systems come with an initial expense for equipment purchase and installation services, it is important to consider their long-term benefits and cost-efficiency. By focusing on the advantages they bring, such as durability, low maintenance requirements, and energy efficiency, businesses can make informed decisions that maximize their return on investment.
High maintenance costs – Pneumatic systems require regular maintenance to ensure they are running correctly and efficiently, which can be costly.
High Maintenance Costs: A Consideration for Pneumatic Systems Installation
While pneumatic systems offer numerous advantages in industrial applications, it is important to consider potential drawbacks as well. One of the cons associated with pneumatic systems installation is the requirement for regular and sometimes costly maintenance.
Pneumatic systems, powered by compressed air, rely on various components such as valves, cylinders, filters, and regulators to function properly. Over time, these components can experience wear and tear due to continuous use or exposure to harsh operating conditions. Regular maintenance is essential to ensure that these components are in optimal condition, preventing system failures and minimizing downtime.
Maintenance tasks for pneumatic systems typically include inspections, lubrication, cleaning or replacing filters, checking for leaks, and adjusting pressure settings. These activities require skilled technicians who have a deep understanding of pneumatic systems and can identify potential issues before they escalate into major problems.
The costs associated with pneumatic system maintenance can vary depending on the complexity of the system and the frequency of required inspections. Additionally, if any components need to be replaced due to wear or damage, there will be additional expenses for purchasing new parts.
However, it is important to note that investing in regular maintenance can actually help businesses save money in the long run. By identifying and addressing minor issues early on through routine inspections, costly breakdowns or extensive repairs can be avoided. Moreover, a well-maintained pneumatic system operates more efficiently, reducing energy consumption and lowering operational costs over time.
To mitigate high maintenance costs associated with pneumatic systems installation, businesses should consider partnering with reputable service providers who specialize in maintaining these systems. These professionals have the expertise and knowledge required to perform thorough inspections and provide timely preventive maintenance services.
In conclusion, while high maintenance costs can be a concern when it comes to pneumatic systems installation, it is crucial to view them as an investment rather than an unnecessary expense. Regular maintenance ensures that these systems operate correctly and efficiently, minimizing downtime and maximizing productivity. By partnering with experienced technicians and adhering to a comprehensive maintenance schedule, businesses can enjoy the benefits of pneumatic systems while effectively managing maintenance costs.
Complex installation process – Installing pneumatic systems can be complex due to the various components that need to be connected together and configured correctly in order for it to work properly.
Complex installation process – A Challenge Worth Overcoming
When it comes to installing pneumatic systems, one challenge that businesses may encounter is the complexity of the installation process. Pneumatic systems consist of various components that need to be connected together and configured correctly in order for the system to function optimally.
The installation process requires careful planning, precise measurements, and a thorough understanding of how the different components interact with each other. From compressors and air filters to regulators, valves, and actuators, each component plays a crucial role in ensuring the smooth operation of the system.
One of the complexities lies in determining the appropriate layout and positioning of these components within the existing infrastructure or machinery. It requires a keen eye for detail and expertise to design an efficient system that minimizes pressure drops, optimizes airflow, and prevents leaks.
Additionally, selecting the right pipe sizes and fittings is essential for maintaining proper air pressure throughout the system. A miscalculation in sizing can lead to inefficiencies or even system failures. It is crucial to consider factors such as flow rates, pressure requirements, and potential expansion needs when making these decisions.
Furthermore, integrating a pneumatic system with existing machinery or equipment can be challenging. Compatibility issues may arise if proper consideration is not given to factors such as power requirements, control interfaces, or communication protocols between different components.
However, while complex installation may seem like a drawback at first glance, it is important to view it as a challenge worth overcoming. Engaging professional installers who specialize in pneumatic systems can greatly alleviate these complexities. Their expertise ensures that all components are properly connected and configured according to industry standards and best practices.
By working with experienced installers who understand the intricacies of pneumatic systems, businesses can navigate through this complexity smoothly. These professionals have the knowledge and skills required to overcome challenges during installation efficiently.
Moreover, investing time and effort into proper installation pays off in the long run. A well-installed pneumatic system ensures optimal performance, minimal downtime, and reduced maintenance requirements. It becomes a reliable tool that enhances productivity and efficiency within the industrial setup.
In conclusion, while the installation process of pneumatic systems may be complex, it is a challenge worth addressing. By engaging professional installers who possess the necessary expertise, businesses can overcome these complexities and reap the benefits of a well-designed and properly functioning pneumatic system. The investment in proper installation ensures that the system operates at its highest efficiency and contributes to the overall success of the business.
Limited scalability – Once installed, it is often difficult or impossible to scale up the system as your needs change over time without having to replace parts or make significant changes in the configuration of the system.
Limited Scalability: A Consideration in Pneumatic Systems Installation
While pneumatic systems offer numerous advantages, it is important to consider potential limitations before committing to their installation. One such limitation is the issue of limited scalability. Once a pneumatic system is installed, it can be challenging or even impossible to scale up the system as needs change over time without significant modifications or part replacements.
The scalability of a system refers to its ability to adapt and expand according to evolving requirements. In the case of pneumatic systems, their scalability can be hindered by various factors. One primary reason is that these systems often require specific components and configurations tailored to their intended purpose during installation.
When businesses experience growth or changes in production demands, they may find themselves needing additional capacity or modifications to their existing pneumatic system. However, due to the nature of pneumatic systems, scaling up can pose challenges. It may involve replacing certain parts, reconfiguring the layout, or even redesigning the entire system.
The need for part replacements or significant changes in configuration can result in increased costs and downtime during the scaling process. It may also disrupt ongoing operations and require additional expertise or resources for successful implementation.
Another aspect that affects scalability is the consideration of space constraints. Pneumatic systems require a dedicated area for their installation, including components such as compressors, air receivers, filters, valves, and actuators. As businesses grow or reconfigure their workspace, accommodating additional components within the existing setup can be challenging.
To mitigate these limitations and ensure future scalability, careful planning during the initial installation phase becomes crucial. Engaging experienced professionals who understand both current requirements and potential future needs can help design a system with some flexibility built-in.
Furthermore, regular maintenance and periodic evaluations of the pneumatic system’s performance can provide insights into its capacity for expansion. By monitoring usage patterns and identifying potential bottlenecks early on, businesses can make informed decisions about necessary modifications or upgrades.
In conclusion, while pneumatic systems offer numerous benefits, it is essential to consider the potential limitations they may pose in terms of scalability. The difficulty or impossibility of scaling up without significant changes or part replacements can impact a business’s ability to adapt to evolving needs. By carefully planning during the installation phase and regularly evaluating system performance, businesses can proactively address scalability concerns and make informed decisions regarding their pneumatic systems.
Limited flexibility – Pneumatic systems are not as flexible as other types of automation systems, meaning that they may not be suitable for applications where frequent changes in the production process are required.
The Limitations of Pneumatic Systems Installation: Limited Flexibility
Pneumatic systems undoubtedly offer numerous advantages in terms of efficiency and performance. However, it is important to acknowledge that they do have certain limitations, one of which is their limited flexibility compared to other types of automation systems.
While pneumatic systems excel in providing reliable and consistent performance for specific applications, they may not be the ideal choice for industries that require frequent changes in the production process. This limitation stems from the nature of compressed air as the power source.
Unlike electrical or hydraulic systems, which can be easily adjusted or reprogrammed to accommodate different tasks or product variations, pneumatic systems rely on a fixed set of components and parameters. Once installed, altering the system’s functionality or adapting it to new requirements can be challenging and time-consuming.
For industries where production lines need to be frequently reconfigured or adapted for different products, pneumatic systems may not provide the desired level of agility. The need for physical adjustments, such as changing valves, actuators, or tubing layouts, can result in significant downtime and increased costs.
Furthermore, the limited flexibility of pneumatic systems can also impact their scalability. Expanding or modifying a pneumatic system to accommodate increased production capacity or new processes may require substantial modifications or even a complete overhaul of the existing setup.
It is worth noting that advancements in technology have led to some improvements in this aspect. Modular pneumatic components and advanced control systems have emerged to address these limitations to some extent. These advancements allow for easier reconfiguration and adaptation of pneumatic systems compared to traditional setups.
Ultimately, when considering whether a pneumatic system is suitable for a particular application, businesses must carefully evaluate their specific needs and requirements. If frequent changes in the production process are anticipated or if scalability is a priority, alternative automation systems such as electrical or hydraulic solutions may offer greater flexibility.
In conclusion, while pneumatic systems offer many benefits in terms of efficiency and performance, they do have limitations, including limited flexibility. Businesses must weigh the advantages and disadvantages of pneumatic systems based on their specific application requirements to make an informed decision about the most suitable automation solution for their needs.
Noise pollution – The operation of pneumatic systems can generate a considerable amount of noise which may disturb people living or working nearby if not adequately soundproofed
Noise Pollution: Addressing the Concerns of Pneumatic Systems Installation
While pneumatic systems offer numerous advantages in industrial settings, it’s important to acknowledge and address potential drawbacks. One notable concern associated with the installation of pneumatic systems is noise pollution. The operation of these systems can generate a considerable amount of noise, which, if not adequately managed, may disturb people living or working nearby.
The compression and release of air in pneumatic systems can produce loud hissing sounds, especially when high pressures are involved. This noise can be disruptive to individuals in close proximity to the system, leading to discomfort and potential productivity issues. In residential areas or workplaces where quiet environments are necessary, uncontrolled noise from pneumatic systems can become a significant problem.
To mitigate the issue of noise pollution caused by pneumatic systems, proper soundproofing measures must be implemented during installation. This involves employing various strategies to minimize sound transmission and ensure a more peaceful environment for everyone involved.
One effective method is the use of sound-insulating materials around the system components that generate the most noise. These materials, such as acoustic enclosures or barriers, absorb or block sound waves from escaping into the surroundings. Additionally, installing vibration-damping mounts for compressors and other equipment can help reduce noise transmission through structural vibrations.
Furthermore, proper maintenance and regular inspections play a crucial role in preventing excessive noise levels. Well-maintained equipment operates more smoothly and efficiently, reducing unnecessary vibrations and minimizing noise output.
It’s worth noting that compliance with local regulations regarding noise levels is essential when installing pneumatic systems. These regulations often set limits on acceptable decibel levels in different areas to protect individuals’ well-being and maintain a harmonious community.
By addressing concerns related to noise pollution during pneumatic system installation, businesses demonstrate their commitment to environmental responsibility and respect for neighboring communities. Moreover, creating quieter work environments can contribute positively towards employee satisfaction and productivity.
In conclusion, while pneumatic systems offer numerous benefits, it is important to acknowledge the potential for noise pollution during their installation. By implementing soundproofing measures, conducting regular maintenance, and adhering to local regulations, businesses can ensure that the operation of pneumatic systems does not disrupt the peace and well-being of those living or working nearby. Striking a balance between the advantages of pneumatic systems and minimizing their impact on noise pollution is key to creating a harmonious coexistence in industrial and residential areas alike.