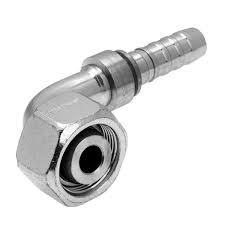
Enhancing Industrial Operations with High-Quality Hose Couplings
The Importance of Hose Couplings in Industrial Applications
Hose couplings are essential components in various industrial applications where the transfer of liquids or gases is required. These fittings play a crucial role in connecting hoses to equipment, ensuring a secure and leak-free connection.
One of the key advantages of hose couplings is their versatility. They come in a wide range of materials, sizes, and configurations to suit different types of hoses and applications. Whether it’s for hydraulic systems, water delivery, or chemical transfer, there is a coupling designed to meet specific requirements.
Another important aspect of hose couplings is their ability to withstand high pressures and temperatures. Industrial operations often involve harsh conditions that put immense stress on equipment. Quality couplings are engineered to handle these challenges, providing a reliable connection that ensures smooth fluid flow.
Proper installation and maintenance of hose couplings are critical to prevent accidents and downtime. Regular inspections can help identify wear and tear early on, allowing for timely replacements and repairs. It’s also essential to follow manufacturer guidelines for assembly and use to maximise the lifespan of the couplings.
In conclusion, hose couplings are indispensable components in industrial settings where fluid transfer is a common requirement. By choosing the right couplings and maintaining them properly, businesses can ensure operational efficiency, safety, and longevity of their equipment.
Seven Key Advantages of Hose Couplings for Robust and Efficient Fluid Management
- Facilitates secure and leak-free connections between hoses and equipment
- Versatile range of materials, sizes, and configurations available to suit different applications
- Can withstand high pressures and temperatures common in industrial operations
- Ensures smooth fluid flow for hydraulic systems, water delivery, and chemical transfer
- Helps prevent accidents and downtime when properly installed and maintained
- Critical component in ensuring operational efficiency in various industries
- Easy to connect and disconnect for quick changes or maintenance
Four Drawbacks of Hose Couplings: Installation Challenges, Specialised Tool Requirements, Cost Considerations, and Compatibility Concerns
- Potential for leaks if not properly installed or maintained
- May require specialized tools for assembly and disassembly
- Some couplings can be expensive, especially high-quality or custom-made ones
- Compatibility issues between different brands or types of couplings
Facilitates secure and leak-free connections between hoses and equipment
Hose couplings play a crucial role in facilitating secure and leak-free connections between hoses and equipment in industrial applications. By providing a tight and reliable seal, these fittings ensure that fluids or gases are transferred efficiently without the risk of leaks or spills. This not only enhances operational safety but also helps maintain the integrity of the system, preventing wastage and potential damage to equipment. Businesses can rely on hose couplings to establish robust connections that promote smooth fluid flow and optimal performance in various industrial processes.
Versatile range of materials, sizes, and configurations available to suit different applications
The versatility of hose couplings, offering a diverse range of materials, sizes, and configurations tailored to specific applications, is a significant advantage in industrial settings. This flexibility allows businesses to select couplings that not only meet their operational requirements but also ensure compatibility with different types of hoses and equipment. Whether it’s for hydraulic systems, chemical transfer, or water delivery, the availability of varied options empowers industries to choose the most suitable coupling for optimal performance and efficiency.
Can withstand high pressures and temperatures common in industrial operations
Hose couplings offer a significant advantage in industrial applications by demonstrating remarkable resilience to the high pressures and temperatures typically encountered in industrial operations. This capability ensures that the couplings maintain a secure and leak-free connection even under challenging conditions, guaranteeing smooth fluid transfer and operational efficiency. Businesses can rely on hose couplings to withstand the rigors of demanding environments, providing a crucial component that contributes to the reliability and safety of their operations.
Ensures smooth fluid flow for hydraulic systems, water delivery, and chemical transfer
Hose couplings play a crucial role in ensuring smooth fluid flow for a variety of applications, including hydraulic systems, water delivery, and chemical transfer. By securely connecting hoses to equipment, couplings help maintain a continuous and efficient flow of liquids or gases without leaks or interruptions. This seamless transfer is essential for the proper functioning of industrial processes, ensuring optimal performance and reliability in various operations.
Helps prevent accidents and downtime when properly installed and maintained
One significant advantage of hose couplings is their ability to help prevent accidents and downtime when installed and maintained correctly. By ensuring a secure and leak-free connection between hoses and equipment, properly installed couplings reduce the risk of leaks, spills, and other safety hazards in industrial settings. Regular maintenance, including inspections and timely replacements when needed, further enhances the reliability of couplings, minimising the chances of unexpected failures that could lead to costly downtime. Overall, the proactive approach to installing and maintaining hose couplings not only promotes a safer working environment but also contributes to uninterrupted operations and increased efficiency.
Critical component in ensuring operational efficiency in various industries
Hose couplings serve as a critical component in ensuring operational efficiency across various industries. By providing a secure and reliable connection between hoses and equipment, couplings facilitate the smooth transfer of liquids or gases, contributing to seamless processes and workflows. Their ability to withstand high pressures and temperatures further enhances efficiency by minimising the risk of leaks or disruptions in fluid flow. In industries where downtime can be costly, the reliability of hose couplings plays a vital role in maintaining productivity and preventing costly delays.
Easy to connect and disconnect for quick changes or maintenance
One significant advantage of hose couplings is their ease of connection and disconnection, making them ideal for quick changes or maintenance tasks. This feature allows for efficient swapping of hoses or equipment without the need for complex tools or prolonged downtime. Whether it’s for replacing a worn-out hose or conducting routine maintenance, the simple and straightforward design of hose couplings enables swift and hassle-free operations, saving valuable time and enhancing productivity in various industrial applications.
Potential for leaks if not properly installed or maintained
One significant drawback of hose couplings is the potential for leaks if they are not correctly installed or adequately maintained. Improper installation, such as insufficient tightening or mismatched fittings, can create gaps that allow fluids to escape, leading to wastage and potential safety hazards. Likewise, neglecting regular maintenance checks can result in wear and tear over time, compromising the integrity of the coupling and increasing the risk of leaks. It is crucial for businesses to prioritise proper installation procedures and routine maintenance to mitigate the risk of leaks and ensure the efficient operation of their industrial systems.
May require specialized tools for assembly and disassembly
One drawback of hose couplings is that they may necessitate the use of specialised tools for both assembly and disassembly. This requirement can add complexity to the maintenance and repair process, potentially leading to delays and increased costs. Moreover, the need for specialised tools may limit the accessibility of servicing tasks to only those with the necessary equipment and expertise, posing a challenge for businesses seeking efficient and cost-effective maintenance solutions.
Some couplings can be expensive, especially high-quality or custom-made ones
One significant drawback of hose couplings is their potential cost, particularly when considering high-quality or custom-made options. While investing in premium couplings can offer superior performance and durability, the upfront expense may pose a financial challenge for businesses operating on tight budgets. Custom-made couplings, designed to meet specific requirements, often come at a higher price point due to the specialised manufacturing processes involved. This cost factor can be a deterrent for some industries looking to balance quality with budget constraints when selecting hose couplings for their operations.
Compatibility issues between different brands or types of couplings
Compatibility issues between different brands or types of hose couplings can pose a significant challenge in industrial applications. When couplings from various manufacturers or with different specifications are used together, there is a risk of leaks, inefficiencies, and even equipment damage. Ensuring proper compatibility is crucial to maintain a seamless fluid transfer system and avoid costly downtime. Businesses must carefully select and standardise their hose couplings to minimise the risk of compatibility issues, thereby promoting smooth operations and enhancing overall safety in the workplace.