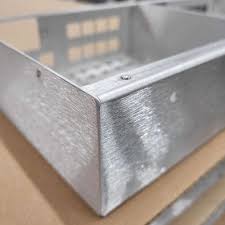
Mastering the Art of All Metal Welding: Techniques and Tips for Success
The Art and Science of All Metal Welding
Welding is a crucial process in metal fabrication, joining two or more metal pieces to create a strong and durable bond. When it comes to all metal welding, the stakes are even higher as it involves working with a wide range of metals, each with its own unique properties and challenges.
One of the key aspects of all metal welding is understanding the different types of metals and their compatibility. From steel and aluminium to titanium and copper, each metal requires specific techniques and considerations to ensure a successful weld.
One of the most common methods used in all metal welding is Tungsten Inert Gas (TIG) welding. This process uses a non-consumable tungsten electrode to create the weld, while an inert gas shield protects the molten weld pool from contamination. TIG welding is known for its precision and ability to weld a wide variety of metals, making it ideal for all metal welding projects.
Another popular technique in all metal welding is Metal Inert Gas (MIG) welding, which uses a consumable wire electrode fed through a welding gun. MIG welding is known for its speed and efficiency, making it suitable for high-volume production environments where productivity is key.
When it comes to all metal welding, proper preparation is essential. This includes cleaning the surfaces to be welded, selecting the right filler material, and ensuring proper ventilation to prevent harmful fumes from accumulating.
At the heart of all metal welding lies the skill and expertise of the welder. A skilled welder understands the nuances of each metal type, knows how to adjust settings for optimal results, and can troubleshoot issues that may arise during the welding process.
In conclusion, all metal welding is both an art and a science that requires precision, knowledge, and experience. By mastering the techniques and understanding the properties of different metals, welders can create strong and reliable bonds that stand the test of time.
Top 5 Essential Tips for Safe and Effective All-Metal Welding
- Ensure proper ventilation when welding metals to prevent inhalation of fumes.
- Use appropriate personal protective equipment, such as welding helmets and gloves.
- Clean the metal surfaces thoroughly before welding to ensure a strong bond.
- Select the correct type of welding technique based on the types of metals being joined.
- Practice good weld bead control and maintain a consistent travel speed for better results.
Ensure proper ventilation when welding metals to prevent inhalation of fumes.
It is crucial to ensure proper ventilation when welding metals to prevent the inhalation of fumes. When metals are welded, especially in the case of all metal welding where a variety of metals may be involved, harmful fumes can be produced. These fumes can contain toxic substances that pose health risks if inhaled. By maintaining adequate ventilation in the welding area, such as using exhaust fans or working in well-ventilated spaces, welders can protect themselves from the potential dangers associated with inhaling welding fumes. Prioritising proper ventilation not only safeguards the welder’s health but also contributes to a safer and more productive welding environment overall.
Use appropriate personal protective equipment, such as welding helmets and gloves.
When engaging in all metal welding, it is crucial to prioritise safety by using appropriate personal protective equipment. Welding helmets and gloves are essential gear that provide protection against intense heat, sparks, and harmful UV rays emitted during the welding process. A welding helmet shields the face and eyes from bright light and potential debris, ensuring the welder’s safety and visibility. Additionally, welding gloves offer protection against burns and cuts while providing a secure grip on welding tools. By wearing the right personal protective equipment, welders can work confidently and safeguard themselves from potential hazards in the welding environment.
Clean the metal surfaces thoroughly before welding to ensure a strong bond.
To achieve a strong and reliable bond in all metal welding, it is crucial to clean the metal surfaces thoroughly before starting the welding process. Removing any dirt, rust, or contaminants from the surfaces ensures proper adhesion and fusion of the metals during welding. Clean metal surfaces promote better penetration of the weld, resulting in a stronger bond that is less prone to defects or failures. By taking the time to clean the metal surfaces diligently, welders can enhance the quality and integrity of their welds, ultimately leading to more robust and durable finished products.
Select the correct type of welding technique based on the types of metals being joined.
When engaging in all metal welding, it is crucial to select the appropriate welding technique based on the types of metals being joined. Different metals have varying properties and behaviours when subjected to heat and pressure, so choosing the right welding method is essential for achieving a strong and durable bond. Whether it’s TIG welding for precision on materials like aluminium or MIG welding for efficiency on steel, matching the welding technique to the specific metals involved ensures a successful weld that meets the required standards of quality and integrity.
Practice good weld bead control and maintain a consistent travel speed for better results.
To achieve optimal results in all metal welding, it is crucial to practice good weld bead control and maintain a consistent travel speed. By controlling the size and shape of the weld bead, welders can ensure proper penetration and fusion between the metal pieces. Consistency in travel speed helps maintain uniform heat distribution, reducing the risk of defects such as burn-through or incomplete fusion. These practices not only improve the quality of the weld but also contribute to overall efficiency and productivity in all metal welding projects.