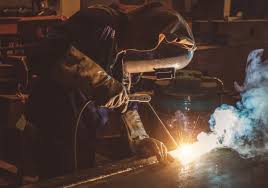
Premium Aluminium Welding Services for Durable Joints
Aluminum Welding Services: The Key to Strong and Durable Joints
Aluminum welding is a specialized process that requires skill, precision, and the right equipment. Whether you are working on automotive components, aerospace parts, or structural elements, choosing the right aluminum welding service is crucial to ensure the strength and durability of your joints.
Aluminum is a lightweight metal known for its high strength-to-weight ratio and corrosion resistance. However, welding aluminum can be challenging due to its low melting point and high thermal conductivity. This is where professional aluminum welding services come into play.
Professional welders who specialize in aluminum welding have the expertise to work with this unique metal effectively. They understand the intricacies of aluminum alloys, heat management techniques, and proper filler materials to create strong and durable welds.
When you opt for aluminum welding services, you can expect:
- High-quality welds that meet industry standards
- Precision and attention to detail in every joint
- Expertise in working with different thicknesses of aluminum
- Efficient turnaround times for your projects
- Strict adherence to safety protocols
Whether you need repairs, fabrication, or custom projects involving aluminum components, professional welding services can deliver the results you need. By entrusting your welding needs to experts in aluminum fabrication, you can ensure that your finished products meet the highest quality standards.
Don’t compromise on the quality of your aluminum welds. Invest in professional aluminum welding services to achieve strong, durable joints that will stand the test of time.
Top 6 Essential Tips for Successful Aluminium Welding Services
- Ensure the aluminium surfaces are clean and free from contaminants before welding.
- Use the appropriate filler material designed for aluminium welding.
- Adjust the welding parameters such as current, voltage, and travel speed for optimal results.
- Consider using a shielding gas like argon to protect the weld pool from atmospheric contamination.
- Preheat thick aluminium pieces to reduce cracking and improve weld quality.
- Practice proper safety measures including wearing protective gear and ensuring good ventilation in the work area.
Ensure the aluminium surfaces are clean and free from contaminants before welding.
To achieve high-quality aluminum welds, it is essential to ensure that the aluminium surfaces are clean and free from contaminants before welding. Contaminants such as dirt, oil, grease, or oxides can negatively impact the integrity of the weld and lead to defects. By meticulously cleaning and preparing the aluminium surfaces prior to welding, you can create a clean environment for optimal heat transfer and bonding, resulting in strong and durable joints that meet industry standards.
Use the appropriate filler material designed for aluminium welding.
When engaging in aluminum welding services, it is essential to use the appropriate filler material specifically designed for aluminium welding. The right filler material ensures proper bonding and strength of the weld, contributing to the longevity and durability of the joint. By selecting the correct filler material tailored for aluminium, welders can achieve high-quality results that meet industry standards and deliver reliable performance in various applications.
Adjust the welding parameters such as current, voltage, and travel speed for optimal results.
To achieve optimal results in aluminum welding services, it is essential to adjust welding parameters such as current, voltage, and travel speed. Fine-tuning these settings is crucial to ensure proper heat input, penetration depth, and overall weld quality. By carefully adjusting these parameters based on the specific requirements of the project and the type of aluminum being welded, welders can achieve strong and durable joints that meet industry standards.
Consider using a shielding gas like argon to protect the weld pool from atmospheric contamination.
When seeking aluminium welding services, it is advisable to consider incorporating a shielding gas such as argon into the process. This gas serves a crucial role in safeguarding the weld pool from atmospheric contamination, ensuring the integrity and quality of the final weld. By utilising argon as a shielding agent, welders can maintain a clean and stable environment during the welding process, ultimately leading to stronger and more durable joints.
Preheat thick aluminium pieces to reduce cracking and improve weld quality.
Preheating thick aluminium pieces before welding is a crucial tip to reduce the risk of cracking and enhance the overall quality of the weld. By preheating the material, you can effectively manage thermal stresses and ensure better fusion between the base metal and filler material. This process helps to minimise distortion and improve the mechanical properties of the weld, resulting in stronger and more durable joints. Incorporating preheating into your aluminium welding process can make a significant difference in achieving high-quality welds that meet industry standards.
Practice proper safety measures including wearing protective gear and ensuring good ventilation in the work area.
To ensure a safe and productive aluminum welding process, it is essential to practice proper safety measures. This includes wearing appropriate protective gear such as welding helmets, gloves, and clothing to shield against sparks and UV radiation. Additionally, maintaining good ventilation in the work area is crucial to prevent the inhalation of harmful fumes and gases produced during the welding process. Prioritising safety not only protects the welder from potential hazards but also contributes to a more efficient and effective welding operation.