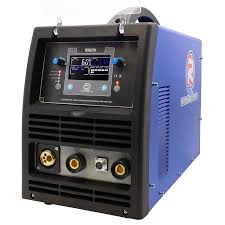
Choosing the Best Welder for Chassis Fabrication: A Comprehensive Guide
The Best Welder for Chassis Fabrication: A Comprehensive Guide
When it comes to chassis fabrication, choosing the right welder is crucial to ensure a strong and durable final product. Welding plays a vital role in joining metal components together to create the frame of a vehicle, making it essential to invest in a high-quality welder that meets the specific requirements of chassis fabrication.
Factors to Consider
There are several factors to consider when selecting the best welder for chassis fabrication:
- Welding Process: The most common welding processes used in chassis fabrication are MIG (Metal Inert Gas) and TIG (Tungsten Inert Gas) welding. Each process has its advantages and limitations, so it’s important to choose a welder that supports the preferred welding method.
- Power Output: The power output of the welder determines its capability to weld different thicknesses of metal. For chassis fabrication, a welder with sufficient power output is essential to ensure strong and consistent welds.
- Duty Cycle: The duty cycle of a welder indicates how long it can operate continuously before needing to cool down. A higher duty cycle is preferable for extended welding sessions typically required in chassis fabrication.
- Portability: Depending on your workspace and mobility needs, you may want to consider the portability of the welder. A lightweight and compact welder can be advantageous for working on various parts of the chassis.
- Budget: While quality should be prioritised, it’s essential to consider your budget when choosing a welder for chassis fabrication. There are various options available at different price points, so finding a balance between cost and features is key.
Top Picks
Based on these factors, some of the best welders for chassis fabrication include:
- Lincoln Electric Power MIG 210 MP Welder: A versatile MIG welder with multi-process capabilities suitable for various welding tasks, including chassis fabrication.
- Miller Electric Syncrowave 210 TIG Welder: An advanced TIG welder known for its precise control and excellent arc performance, ideal for intricate welding on chassis components.
- Hobart Handler 140 MIG Welder: An affordable yet reliable MIG welder that offers good power output and ease of use, making it suitable for beginners in chassis fabrication.
In Conclusion
Selecting the best welder for chassis fabrication requires careful consideration of factors such as welding process, power output, duty cycle, portability, and budget. By choosing a high-quality welder that aligns with your specific needs and preferences, you can ensure efficient and precise welding results in creating durable vehicle frames.
Investing in the right equipment is key to achieving success in chassis fabrication projects. With the proper tools at your disposal, you can confidently tackle any welding task with precision and skill.
Top 5 FAQs on Choosing the Best Welder for Chassis Fabrication
- What type of welder is used for fabrication?
- What size welder do I need to weld a car frame?
- What type of welder is best for automotive work?
- What type of welding is used for chassis?
- Is MIG or TIG better for fabrication?
What type of welder is used for fabrication?
When it comes to fabrication, the type of welder used plays a significant role in determining the quality and strength of the final product. For chassis fabrication specifically, welders commonly utilise MIG (Metal Inert Gas) and TIG (Tungsten Inert Gas) welding processes. MIG welding is favoured for its speed and ease of use, making it suitable for welding thicker materials typically found in chassis construction. On the other hand, TIG welding offers precise control and produces clean welds, making it ideal for intricate and detailed work on chassis components. The choice between MIG and TIG welders ultimately depends on the specific requirements of the fabrication project, with both types offering unique advantages to ensure strong and durable welds in chassis construction.
What size welder do I need to weld a car frame?
When determining the size of welder needed to weld a car frame, several factors come into play. The thickness of the metal being welded, the welding process used (such as MIG or TIG), and the type of joints being created all influence the size of welder required. For welding a car frame, a welder with sufficient power output, typically ranging from 140 to 200 amps for MIG welding and 150 to 250 amps for TIG welding, is recommended to ensure strong and reliable welds. It’s essential to match the size of the welder with the specific requirements of the car frame fabrication project to achieve optimal results in terms of strength and durability.
What type of welder is best for automotive work?
When it comes to automotive work, the type of welder that is best suited for the job is often dependent on the specific requirements of the project. However, for chassis fabrication and other automotive applications, MIG (Metal Inert Gas) welding is commonly preferred due to its versatility, ease of use, and ability to produce strong and clean welds. MIG welders are well-suited for welding various metals typically found in automotive components, making them a popular choice among professionals and enthusiasts alike. Additionally, TIG (Tungsten Inert Gas) welding is also favoured for its precision and control, making it ideal for intricate welding tasks on automotive parts that require high-quality finishes. Ultimately, selecting the best welder for automotive work involves considering factors such as the type of materials being welded, the desired welding technique, and the overall project requirements to ensure optimal results.
What type of welding is used for chassis?
In chassis fabrication, the type of welding commonly used is MIG (Metal Inert Gas) welding and TIG (Tungsten Inert Gas) welding. MIG welding is favoured for its speed and ease of use, making it suitable for joining thicker metal components in chassis construction. On the other hand, TIG welding is preferred for its precision and clean welds, making it ideal for intricate and detailed work on chassis components where aesthetics and strength are crucial. Both welding processes have their advantages and are commonly employed in chassis fabrication to ensure strong, durable, and high-quality welds that form the foundation of a reliable vehicle frame.
Is MIG or TIG better for fabrication?
When it comes to chassis fabrication, the choice between MIG (Metal Inert Gas) and TIG (Tungsten Inert Gas) welding often sparks the debate on which method is better suited for the job. While both techniques have their own strengths and applications, the decision ultimately depends on the specific requirements of the fabrication project. MIG welding is known for its speed and efficiency in welding thicker materials, making it a popular choice for chassis fabrication where structural integrity is paramount. On the other hand, TIG welding offers superior control and precision, making it ideal for intricate welds on thinner materials commonly found in chassis components. Ultimately, the best welder for chassis fabrication depends on factors such as material thickness, desired finish, and personal preference in handling different welding processes.