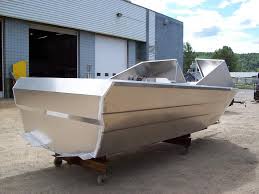
Crafting Precision and Durability: The Art of Custom Aluminium Welding
Custom Aluminium Welding: Crafting Precision and Durability
Aluminium is a versatile metal known for its lightweight properties and exceptional strength. When it comes to custom fabrication, aluminium welding plays a crucial role in creating bespoke structures that require precision and durability.
Custom aluminium welding involves the process of joining aluminium pieces together using specialised techniques such as TIG (Tungsten Inert Gas) welding or MIG (Metal Inert Gas) welding. These methods allow welders to create seamless bonds that are both strong and aesthetically pleasing.
One of the key advantages of custom aluminium welding is the ability to tailor designs to specific requirements. Whether it’s creating intricate components for aerospace applications or crafting durable frames for automotive parts, custom aluminium welding offers endless possibilities for innovation.
Furthermore, aluminium is highly resistant to corrosion, making it an ideal choice for outdoor structures or marine applications where exposure to moisture is a concern. Custom aluminium welding ensures that joints are properly sealed, providing long-lasting protection against environmental elements.
At XYZ Welding Services, we specialise in custom aluminium welding, offering our clients bespoke solutions that meet their unique needs. Our team of skilled welders has extensive experience working with aluminium and can deliver high-quality results that exceed expectations.
Whether you require custom aluminium welding for architectural projects, industrial machinery, or specialised components, our dedicated team is ready to assist you. We take pride in our craftsmanship and attention to detail, ensuring that every weld is executed with precision and care.
In conclusion, custom aluminium welding is a valuable process that opens up a world of possibilities for creating bespoke structures with exceptional strength and durability. With the right expertise and techniques, custom aluminium welding can transform your vision into reality.
Exploring the Advantages of Custom Aluminium Welding: Lightweight, Strong, and Versatile Solutions
- 1. Lightweight
- 2. Strength
- 3. Corrosion resistance
- 4. Precision
- 5. Aesthetically pleasing
- 6. Versatility
Challenges and Costs of Custom Aluminium Welding: Key Considerations
- High initial setup costs for equipment and training
- Requires skilled welders with expertise in aluminium welding techniques
- Aluminium welding can be more challenging than welding other metals due to its heat conductivity
- Potential for distortion or warping of aluminium parts during the welding process
1. Lightweight
Aluminium’s lightweight properties make custom aluminium welding an ideal choice for applications where weight is a critical factor. Whether it’s for aerospace components, automotive parts, or structural elements, the use of aluminium allows for the creation of durable and strong structures without adding unnecessary weight. This advantage not only enhances performance but also contributes to improved fuel efficiency and overall efficiency in various industries. Custom aluminium welding offers a solution that combines strength with lightweight characteristics, making it a preferred option for projects where weight savings are essential.
2. Strength
Custom aluminium welding offers the significant advantage of strength. By creating strong and durable bonds, custom aluminium welding ensures the structural integrity of fabricated components. This means that the resulting structures are not only sturdy but also capable of withstanding various stresses and environmental conditions, making them reliable and long-lasting solutions for a wide range of applications.
3. Corrosion resistance
Custom aluminium welding offers a significant advantage in terms of corrosion resistance. Aluminium’s innate ability to withstand corrosion makes it an ideal choice for outdoor and marine applications where exposure to moisture and harsh environmental conditions is common. By utilising custom aluminium welding techniques, structures can be crafted with enhanced longevity and durability, ensuring that they maintain their integrity even in challenging settings.
4. Precision
Custom aluminium welding offers a significant advantage in terms of precision, enabling the fabrication of intricate designs and components to exact specifications. This level of precision is essential for industries where accuracy is paramount, such as aerospace and automotive sectors. With custom aluminium welding, skilled welders can create complex structures with tight tolerances, ensuring that every detail aligns perfectly with the desired outcome. This precision ultimately leads to high-quality results that meet and exceed the specific requirements of each project.
5. Aesthetically pleasing
One of the key advantages of custom aluminium welding is its ability to produce aesthetically pleasing results. By utilising advanced welding techniques, such as TIG or MIG welding, aluminium welders can create seamless joints that not only ensure structural integrity but also enhance the visual appeal of the finished products. The clean and smooth finish achieved through custom aluminium welding adds a touch of sophistication to any project, making it a popular choice for industries where both functionality and aesthetics are paramount.
6. Versatility
Custom aluminium welding showcases remarkable versatility, presenting a pro that opens up a realm of creative possibilities and innovation. This process enables the crafting of bespoke structures that are precisely tailored to meet unique requirements, highlighting the adaptability and flexibility that custom aluminium welding brings to various industries and applications.
High initial setup costs for equipment and training
One significant drawback of custom aluminium welding is the high initial setup costs associated with acquiring specialized equipment and providing training for skilled welders. The investment required to procure advanced welding machinery and ensure that personnel are adequately trained can pose a financial challenge for businesses looking to venture into custom aluminium welding. These upfront expenses can deter smaller enterprises or individuals from entering the market, limiting their ability to take advantage of the benefits that custom aluminium welding offers in terms of precision and durability.
Requires skilled welders with expertise in aluminium welding techniques
One significant drawback of custom aluminium welding is the requirement for skilled welders with expertise in aluminium welding techniques. Working with aluminium presents unique challenges due to its properties, such as high thermal conductivity and low melting point. Welders must possess a deep understanding of the metal’s behaviour during welding, as well as proficiency in specialised techniques like TIG and MIG welding. Without skilled welders who have mastered the intricacies of aluminium welding, achieving high-quality and durable welds can be challenging and may result in compromised structural integrity.
Aluminium welding can be more challenging than welding other metals due to its heat conductivity
Aluminium welding presents a significant challenge compared to welding other metals due to its high heat conductivity. The rapid dissipation of heat in aluminium makes it more difficult to maintain the precise temperature required for a successful weld. Welders must carefully monitor and adjust their techniques to account for this heat conductivity, ensuring that the material reaches the optimal melting point without overheating or warping. This added complexity in managing heat can make aluminium welding a more intricate and demanding process, requiring a skilled and experienced welder to achieve high-quality results.
Potential for distortion or warping of aluminium parts during the welding process
During the custom aluminium welding process, one significant drawback is the potential for distortion or warping of aluminium parts. Due to the high heat involved in welding aluminium, the metal can expand and contract unevenly, leading to misalignment or deformation of the welded components. This distortion can impact the overall structural integrity and aesthetics of the final product, requiring additional time and effort to correct and restore the original shape. Careful planning and precise techniques are essential to minimise distortion and ensure that custom aluminium welding results in a flawless finish.