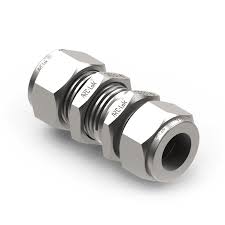
Mastering the Art of Instrument Pipe Fitting: Precision and Expertise in Industrial Applications
Instrument Pipe Fitting: Precision and Expertise
Instrument pipe fitting is a critical aspect of various industries, including oil and gas, chemical processing, and manufacturing. It involves the installation, maintenance, and repair of piping systems that carry liquids or gases in industrial settings.
One of the key components of instrument pipe fitting is precision. Every measurement, cut, and connection must be made with utmost accuracy to ensure the proper functioning of the piping system. A small error in fitting can lead to leaks, inefficiencies, or even safety hazards.
Expertise is another essential element in instrument pipe fitting. Skilled fitters have a deep understanding of different types of pipes, fittings, and materials used in industrial applications. They are proficient in reading technical drawings and blueprints to execute complex installations with efficiency and accuracy.
Instrument pipe fitting requires a combination of technical knowledge, practical skills, and attention to detail. Fitters must be able to work in challenging environments, often under tight deadlines and strict safety regulations.
Whether it’s installing a new pipeline or repairing an existing system, instrument pipe fitting plays a crucial role in ensuring the smooth operation of industrial facilities. Skilled fitters are invaluable assets to companies looking to maintain their infrastructure at peak performance.
In conclusion, instrument pipe fitting is a specialised field that demands precision, expertise, and dedication. The work of skilled fitters is essential for the success and safety of various industries that rely on efficient piping systems.
Essential FAQs on Instrument Pipe Fitting: Understanding Types, Precision, Qualifications, and Standards
- What is instrument pipe fitting?
- What are the common types of pipes used in instrument pipe fitting?
- How important is precision in instrument pipe fitting?
- What qualifications are required to become an instrument pipe fitter?
- What safety measures should be followed during instrument pipe fitting?
- How do you read technical drawings and blueprints for instrument pipe fitting?
- What are the typical challenges faced in instrument pipe fitting?
- How can one ensure the proper maintenance of piping systems after installation?
- Are there any industry standards or regulations that govern instrument pipe fitting?
What is instrument pipe fitting?
Instrument pipe fitting refers to the process of installing, maintaining, and repairing piping systems that are specifically designed to carry liquids or gases in industrial settings. It involves the precise connection of pipes, valves, fittings, and other components to ensure the proper functioning of instruments used in various industries such as oil and gas, chemical processing, and manufacturing. Instrument pipe fitting requires a high level of accuracy and expertise to guarantee that the piping system operates efficiently and safely. Skilled fitters play a crucial role in ensuring that these intricate systems are installed correctly and maintained to industry standards.
What are the common types of pipes used in instrument pipe fitting?
In instrument pipe fitting, several common types of pipes are used to ensure the proper functioning of industrial piping systems. Some of the most frequently employed pipe materials include stainless steel, carbon steel, copper, and PVC. Stainless steel pipes are known for their durability and resistance to corrosion, making them ideal for applications requiring high strength and longevity. Carbon steel pipes are widely used for their affordability and versatility in various industrial settings. Copper pipes are preferred for their excellent heat conductivity and resistance to corrosion, often used in HVAC systems. PVC pipes, on the other hand, are lightweight and cost-effective options suitable for low-pressure applications. Understanding the characteristics and benefits of each type of pipe is crucial in selecting the most appropriate material for instrument pipe fitting projects.
How important is precision in instrument pipe fitting?
Precision in instrument pipe fitting is absolutely crucial for the successful operation and safety of industrial piping systems. Even the smallest deviation from accurate measurements or alignments can lead to leaks, inefficiencies, and potential hazards. Precision ensures that pipes fit together seamlessly, allowing for smooth flow and optimal performance. Skilled fitters understand the significance of precision in every aspect of their work, from cutting pipes to making connections, as it directly impacts the reliability and longevity of the entire system. In instrument pipe fitting, precision is not just a preference but a fundamental requirement for ensuring the integrity and functionality of industrial piping networks.
What qualifications are required to become an instrument pipe fitter?
To become an instrument pipe fitter, certain qualifications are typically required. These may include completing a relevant vocational training programme or apprenticeship to gain hands-on experience and technical knowledge in pipe fitting. Additionally, obtaining certifications in areas such as welding, plumbing, or mechanical engineering can enhance one’s credentials as an instrument pipe fitter. Strong mathematical skills, attention to detail, and the ability to interpret technical drawings are also essential for success in this field. Overall, a combination of formal education, practical training, and relevant certifications is key to becoming a qualified instrument pipe fitter.
What safety measures should be followed during instrument pipe fitting?
When it comes to instrument pipe fitting, ensuring safety is paramount. Several key safety measures should be followed during the fitting process to prevent accidents and protect both workers and the surrounding environment. These measures include wearing appropriate personal protective equipment (PPE) such as gloves, safety glasses, and steel-toed boots to reduce the risk of injuries. Prioritising proper ventilation in confined spaces is crucial to prevent exposure to hazardous gases. Additionally, following strict lockout/tagout procedures to control energy sources and conducting thorough risk assessments before starting any fitting work are essential steps in maintaining a safe working environment during instrument pipe fitting operations.
How do you read technical drawings and blueprints for instrument pipe fitting?
Understanding how to read technical drawings and blueprints is crucial for successful instrument pipe fitting. These documents provide detailed information on the layout, dimensions, materials, and connections required for a piping system. Fitters must be able to interpret symbols, annotations, and measurements accurately to ensure precise installation and alignment of pipes and fittings. By studying these drawings carefully, fitters can plan their work effectively, identify potential challenges in advance, and execute the fitting process with the precision and expertise necessary for a successful outcome.
What are the typical challenges faced in instrument pipe fitting?
Instrument pipe fitting presents several challenges that fitters commonly encounter. One of the main difficulties is ensuring precise measurements and alignments to avoid leaks or inefficiencies in the piping system. Fitters must also navigate complex installations in tight spaces, often requiring them to work in confined or hazardous environments. Additionally, staying up-to-date with evolving industry standards and technologies poses a challenge, as fitters need to adapt their skills and knowledge to meet changing requirements. Overall, the demanding nature of instrument pipe fitting calls for skilled professionals who can overcome these challenges with precision and expertise.
How can one ensure the proper maintenance of piping systems after installation?
Ensuring the proper maintenance of piping systems after installation is crucial for their long-term performance and reliability. Regular inspection and maintenance schedules should be established to detect any potential issues early on. This includes checking for leaks, corrosion, or any signs of wear and tear. Proper cleaning and flushing of the pipes can help prevent blockages and ensure smooth flow. Additionally, keeping detailed records of maintenance activities and conducting periodic tests can help identify any emerging problems before they escalate. By investing in proactive maintenance measures, one can prolong the lifespan of piping systems and avoid costly repairs in the future.
Are there any industry standards or regulations that govern instrument pipe fitting?
In the realm of instrument pipe fitting, adherence to industry standards and regulations is paramount. Various governing bodies, such as the American Society of Mechanical Engineers (ASME) and the International Organization for Standardization (ISO), have established stringent guidelines to ensure the safety, quality, and efficiency of piping systems. These standards cover aspects like material specifications, installation procedures, testing requirements, and compliance with environmental and safety protocols. Fitters must stay abreast of these regulations to guarantee that their work meets the highest industry standards and contributes to the overall integrity of industrial piping systems.