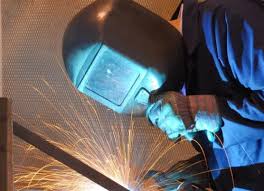
Bespoke Solutions: The Art of Custom Welding and Fabrication
Custom Welding and Fabrication: Crafting Quality Solutions
Custom welding and fabrication play a crucial role in various industries, from construction to automotive to manufacturing. These processes involve the skilled manipulation of metal to create bespoke components and structures that meet specific requirements.
One of the key benefits of custom welding and fabrication is the ability to tailor products to exact specifications. This flexibility allows businesses to design unique solutions that are not readily available off-the-shelf. Whether it’s a custom-built frame for a machinery or a specialised part for an industrial application, custom welding and fabrication can deliver precise results.
Skilled welders and fabricators use a variety of techniques, such as MIG welding, TIG welding, and arc welding, to join metal pieces together. They work with different types of metals, including steel, aluminium, and stainless steel, depending on the project requirements.
Quality is paramount in custom welding and fabrication. Experienced professionals pay attention to detail and precision throughout the process to ensure the final product meets high standards. From initial design concepts to final inspection, every step is carefully executed to deliver durable and reliable components.
Custom welding and fabrication also offer cost-effective solutions for businesses. By creating bespoke parts that fit specific needs, companies can avoid unnecessary expenses associated with modifying standard products or dealing with compatibility issues.
In conclusion, custom welding and fabrication provide a versatile approach to creating tailored metal components for various industries. With skilled craftsmanship, attention to detail, and a commitment to quality, these processes offer innovative solutions that meet the unique demands of modern businesses.
Essential FAQs on Custom Welding and Fabrication: A Comprehensive Guide
- What is custom welding and fabrication?
- What industries commonly use custom welding and fabrication services?
- What materials can be used in custom welding and fabrication?
- How does custom welding differ from standard welding services?
- What are the benefits of opting for custom welding and fabrication over pre-made components?
- How long does a typical custom welding project take to complete?
- What qualifications or certifications should I look for in a custom welder or fabricator?
- Can custom welding and fabrication services be tailored to specific budget constraints?
- Are there any maintenance requirements for products created through custom welding and fabrication?
What is custom welding and fabrication?
Custom welding and fabrication refer to the specialised processes of crafting bespoke metal components and structures to meet specific requirements. Skilled welders and fabricators use various techniques to join metal pieces together, creating custom-built solutions tailored to individual needs. From designing unique parts to executing precise welds, custom welding and fabrication ensure that businesses can obtain high-quality, made-to-order products that are not readily available off-the-shelf.
What industries commonly use custom welding and fabrication services?
Custom welding and fabrication services are in high demand across a range of industries that require bespoke metalwork solutions. Industries commonly utilising these services include construction, where custom metal structures and components are vital for building projects. The automotive industry also relies on custom welding and fabrication for creating specialised parts and prototypes. Manufacturing sectors benefit from custom metalwork for machinery, equipment, and tooling needs. Additionally, industries such as aerospace, marine, and energy sectors often turn to custom welding and fabrication services to meet their unique requirements with precision and quality craftsmanship.
What materials can be used in custom welding and fabrication?
In custom welding and fabrication, a wide range of materials can be used to create bespoke components and structures tailored to specific requirements. Common materials include steel, aluminium, stainless steel, copper, brass, and titanium. Each material has its unique properties and characteristics that make it suitable for different applications. Whether it’s the strength of steel for structural components or the corrosion resistance of stainless steel for outdoor installations, the choice of material plays a crucial role in determining the performance and durability of the final product. Skilled welders and fabricators understand how to work with these materials effectively to achieve optimal results in custom welding and fabrication projects.
How does custom welding differ from standard welding services?
Custom welding differs from standard welding services in that it involves the fabrication of unique, tailor-made metal components to meet specific requirements. While standard welding services focus on joining metal pieces together based on pre-existing designs or templates, custom welding requires a more intricate and personalised approach. Skilled welders and fabricators in custom welding pay close attention to detail, precision, and innovation to create bespoke solutions that are not readily available off-the-shelf. This process allows for greater flexibility, creativity, and the ability to address individual needs with a high level of craftsmanship and expertise.
What are the benefits of opting for custom welding and fabrication over pre-made components?
Opting for custom welding and fabrication over pre-made components offers a range of benefits. Custom solutions allow businesses to tailor products to exact specifications, ensuring they meet specific requirements with precision. This flexibility enables the creation of unique designs that may not be readily available off-the-shelf. Skilled welders and fabricators can use their expertise to craft bespoke components that are durable, reliable, and perfectly suited to the intended application. By choosing custom welding and fabrication, businesses can avoid the limitations of pre-made components and instead enjoy cost-effective solutions that are tailored to their individual needs.
How long does a typical custom welding project take to complete?
The duration of a typical custom welding project can vary depending on several factors, including the complexity of the design, the size of the project, the type of materials being used, and the availability of resources. While some smaller projects may be completed within a few days or weeks, larger and more intricate custom welding projects could take several weeks or even months to finish. It is essential for businesses and individuals seeking custom welding services to discuss timelines and deadlines with their chosen welder or fabricator to ensure clear communication and alignment on project expectations.
What qualifications or certifications should I look for in a custom welder or fabricator?
When seeking a custom welder or fabricator, it is essential to consider their qualifications and certifications to ensure the quality of workmanship. Look for professionals who hold relevant certifications such as welding certifications (e.g., AWS certification) and qualifications in metal fabrication techniques. These credentials indicate that the welder or fabricator has undergone formal training and possesses the necessary skills to perform custom welding and fabrication tasks effectively. Additionally, certifications in health and safety practices demonstrate a commitment to workplace safety, which is crucial in industrial settings. By prioritising qualified and certified professionals, you can have confidence in the expertise and reliability of your chosen custom welder or fabricator.
Can custom welding and fabrication services be tailored to specific budget constraints?
Custom welding and fabrication services can indeed be tailored to specific budget constraints. Skilled professionals in the industry understand the importance of cost-effectiveness and work closely with clients to find solutions that align with their financial parameters. By offering flexible options, such as material choices, design modifications, and efficient production processes, custom welding and fabrication services can accommodate varying budgets without compromising on quality or precision. This collaborative approach ensures that clients receive bespoke metalwork solutions that not only meet their requirements but also fit within their budgetary considerations.
Are there any maintenance requirements for products created through custom welding and fabrication?
Maintenance requirements for products created through custom welding and fabrication largely depend on the specific materials used, the environment in which the products are placed, and the intended usage. Generally, regular inspections for signs of wear, corrosion, or structural integrity are recommended to ensure the longevity and performance of custom-welded components. Proper cleaning, lubrication, and protective coatings may also be necessary to prevent deterioration over time. It is advisable to follow any maintenance guidelines provided by the fabricator or consult with industry experts to determine the best practices for preserving the quality of custom-welded products.