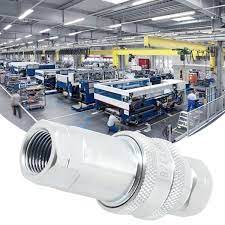
Precision and Safety: Mastering Industrial Machinery Fitting for Efficient Manufacturing
Industrial Machinery Fitting: Ensuring Efficiency and Safety in Manufacturing
In the world of manufacturing, industrial machinery fitting plays a crucial role in ensuring the smooth operation of production processes. From assembly lines to heavy-duty equipment, skilled fitters are responsible for installing, maintaining, and repairing machinery to keep businesses running efficiently and safely.
The primary objective of industrial machinery fitting is to ensure that all components of a machine are properly installed and aligned. This precision work requires a deep understanding of mechanical systems, electrical circuits, and hydraulic or pneumatic systems. Fitters must possess a wide range of technical skills to handle various types of machinery effectively.
One key aspect of industrial machinery fitting is the installation process. Fitters carefully analyze blueprints and technical specifications to determine the optimal positioning of each component. They meticulously assemble parts, connect electrical wiring, calibrate sensors, and test functionality to guarantee that everything operates as intended.
Moreover, maintenance is an ongoing responsibility for fitters. Regular inspections are conducted to identify potential issues before they escalate into costly breakdowns or accidents. By conducting preventive maintenance tasks such as lubrication, realignment, and replacement of worn-out parts, fitters ensure that machines continue operating at peak performance levels.
Inevitably, breakdowns can occur even with proper maintenance. When this happens, fitters step in to troubleshoot problems and make necessary repairs swiftly. Their expertise allows them to diagnose faults accurately and implement effective solutions efficiently. This minimizes downtime and helps businesses maintain their production schedules without significant interruptions.
Safety is paramount in any industrial environment. Industrial machinery fitting also involves adhering to strict safety regulations during installation and maintenance procedures. Fitters must be knowledgeable about safety protocols such as lockout/tagout procedures (LOTO), which safeguard workers from accidental startup or release of stored energy during servicing activities.
Furthermore, fitters play an essential role in promoting workplace safety by identifying potential hazards associated with machinery operations. They collaborate with engineers and safety professionals to implement safety measures, such as installing guards, emergency stop systems, or implementing interlocks to prevent unauthorized access.
In conclusion, industrial machinery fitting is a critical component of the manufacturing industry. Skilled fitters ensure that machinery is installed correctly, maintained regularly, and repaired promptly to maximize efficiency and productivity. Their expertise not only keeps businesses running smoothly but also safeguards the well-being of workers by adhering to strict safety standards.
If you are a business owner in need of reliable industrial machinery fitting services or an aspiring fitter looking for a challenging career path, it is crucial to recognize the importance of this profession. By investing in skilled fitters and prioritizing their role within your organization, you can ensure optimal performance and safety in your manufacturing processes.
Title: The Advantages of Industrial Machinery Fitting in the UK
- Increased Efficiency – Industrial machinery fitting helps to increase the efficiency of production processes, as it ensures that all components are properly fitted and work together in harmony.
- Reduced Maintenance Costs – By using industrial machinery fitting, businesses are able to reduce their maintenance costs as the machines will be less prone to breakdowns due to incorrect or loose fittings.
- Improved Safety – The correct installation of industrial machinery can improve safety on the factory floor by reducing the risk of accidents caused by faulty equipment or incorrect fittings.
- Improved Product Quality – By ensuring that all parts are properly fitted and working correctly, businesses can ensure that their products meet high standards of quality and consistency.
- Cost Savings – Industrial machinery fitting can help companies save money in the long run as they will not need to replace faulty equipment or pay for expensive repairs due to improper installation.
Challenges in Industrial Machinery Fitting: Exploring the Downsides
- High cost of installation and maintenance
- Risk of injury due to improper handling
- Noise pollution from machinery operation
- Limited access to parts and components
- Potential environmental hazards from emissions
Increased Efficiency – Industrial machinery fitting helps to increase the efficiency of production processes, as it ensures that all components are properly fitted and work together in harmony.
Increased Efficiency: The Power of Industrial Machinery Fitting
In the fast-paced world of manufacturing, efficiency is key to staying competitive. Industrial machinery fitting plays a vital role in achieving this efficiency by ensuring that all components of a machine are properly fitted and work together seamlessly.
When it comes to production processes, every second counts. A poorly fitted machine can lead to unnecessary downtime, delays, and decreased productivity. However, with the expertise of skilled fitters, businesses can optimize their operations and maximize output.
Industrial machinery fitting involves meticulous attention to detail. Fitters carefully analyze blueprints and technical specifications to ensure that each component is installed correctly and aligned precisely. This precision work guarantees that the machine functions as intended, minimizing errors and reducing the need for rework.
By having properly fitted machinery, businesses can streamline their production processes. Components operate smoothly without unnecessary friction or misalignment issues, allowing for faster and more efficient operation. This increased efficiency translates into higher productivity levels and ultimately leads to cost savings.
Moreover, properly fitted machinery reduces the risk of breakdowns or malfunctions during operation. When all components are aligned correctly, stress on individual parts is minimized. This reduces wear and tear on the machine over time, prolonging its lifespan and reducing the frequency of maintenance or repairs needed.
Efficiency gains from industrial machinery fitting are not limited to assembly lines or manufacturing plants alone. It extends to various industries such as construction, energy production, automotive manufacturing, and more. Whether it’s a large-scale industrial machine or a complex piece of equipment, proper fitting ensures optimal performance across different sectors.
Additionally, increased efficiency in production processes positively impacts product quality. When machines function smoothly without any glitches or inconsistencies caused by poor fitting, the end product meets or exceeds customer expectations consistently. This helps build trust with clients and enhances the reputation of businesses in their respective industries.
In conclusion, industrial machinery fitting brings forth increased efficiency in production processes by ensuring proper alignment and functionality of all machine components. From reducing downtime to improving product quality, the impact of proper fitting is far-reaching. By investing in skilled fitters and prioritizing the fitting process, businesses can unlock the full potential of their machinery, stay ahead of the competition, and achieve sustainable growth.
Reduced Maintenance Costs – By using industrial machinery fitting, businesses are able to reduce their maintenance costs as the machines will be less prone to breakdowns due to incorrect or loose fittings.
Reduced Maintenance Costs: The Benefits of Industrial Machinery Fitting
In the fast-paced world of manufacturing, businesses are always seeking ways to optimize their operations and minimize costs. One significant advantage of industrial machinery fitting is its ability to reduce maintenance expenses. By ensuring that machines are correctly fitted and all components are tightly secured, businesses can significantly decrease the frequency of breakdowns caused by loose or incorrect fittings.
When industrial machinery is not properly fitted, it can lead to a range of issues. Loose fittings can result in vibrations, misalignments, or excessive wear on components. Over time, these problems can escalate and cause breakdowns or malfunctions that require costly repairs. Additionally, improper fittings may also lead to safety hazards for workers operating the machinery.
By utilizing professional fitters who possess expertise in industrial machinery fitting, businesses can mitigate these risks. Skilled fitters meticulously analyze blueprints and technical specifications to ensure precise installation and alignment of all components. They tighten bolts, connect electrical wiring securely, and verify that all parts function harmoniously as intended.
The result is a well-fitted machine that operates smoothly and efficiently. Properly aligned components reduce vibrations and minimize wear on moving parts. This not only extends the lifespan of the machinery but also reduces the likelihood of unexpected breakdowns or malfunctions.
By reducing maintenance costs through industrial machinery fitting, businesses can allocate their resources more effectively. Instead of constantly dealing with expensive repairs or unplanned downtime due to equipment failures, they can focus on proactive maintenance strategies and invest in other areas of their operations.
Moreover, minimizing breakdowns also leads to increased productivity. When machines are operating optimally without frequent interruptions for repairs, production schedules can be maintained consistently. This helps meet customer demands promptly while maximizing output efficiency.
Additionally, reducing maintenance costs positively impacts worker safety. Well-fitted machinery decreases the chances of accidents caused by loose parts or sudden failures during operation. By prioritizing proper fittings through professional industrial machinery fitting, businesses demonstrate their commitment to providing a safe working environment for their employees.
In conclusion, the reduced maintenance costs associated with industrial machinery fitting offer significant advantages for businesses. By ensuring that machines are correctly installed and all components are tightly secured, the frequency of breakdowns due to loose or incorrect fittings is greatly reduced. This not only saves businesses money on repairs but also improves productivity and promotes worker safety.
Investing in professional fitters who possess the necessary expertise in industrial machinery fitting can lead to long-term cost savings and operational efficiency. By prioritizing proper fittings, businesses can enjoy the benefits of reliable machinery that operates smoothly and minimizes unexpected downtime.
Improved Safety – The correct installation of industrial machinery can improve safety on the factory floor by reducing the risk of accidents caused by faulty equipment or incorrect fittings.
Improved Safety: The Crucial Role of Industrial Machinery Fitting
In the fast-paced world of manufacturing, safety is a top priority. Industrial machinery fitting plays a crucial role in ensuring the safety of workers on the factory floor. By correctly installing machinery and ensuring proper fittings, the risk of accidents caused by faulty equipment or incorrect installations is significantly reduced.
One of the key advantages of industrial machinery fitting is its contribution to improved safety standards. Skilled fitters have a deep understanding of machinery components, electrical systems, and mechanical operations. They meticulously follow technical specifications and blueprints to ensure that every part is installed correctly and aligned precisely.
By adhering to strict installation procedures, fitters minimize the risk of accidents that can result from faulty equipment. Improperly installed machinery can lead to malfunctions, breakdowns, or even catastrophic failures, putting workers’ lives at risk. However, with skilled fitters overseeing the installation process, these risks are mitigated.
Moreover, industrial machinery fitting involves thorough testing and calibration to ensure optimal functionality. Fitters meticulously check electrical connections, mechanical alignments, and sensor accuracy to guarantee that everything operates as intended. This attention to detail significantly reduces the chances of unexpected malfunctions or accidents caused by incorrect fittings.
Regular maintenance is another aspect where improved safety comes into play. Skilled fitters conduct routine inspections to identify potential issues before they escalate into major problems. By addressing minor faults promptly through preventive maintenance measures such as realignment or part replacement, they prevent more significant breakdowns that could pose serious safety risks.
In addition to preventing accidents caused by faulty equipment or incorrect fittings, industrial machinery fitting professionals also contribute to workplace safety by identifying potential hazards associated with specific machines or processes. Their expertise allows them to implement additional safety measures such as installing guards or emergency stop systems in areas where there may be a higher risk of injury.
Ultimately, investing in skilled fitters for industrial machinery fitting not only ensures efficient operations but also creates a safer working environment for employees. By reducing the risk of accidents caused by faulty equipment or incorrect fittings, businesses can minimize downtime, maintain productivity, and most importantly, protect the well-being of their workforce.
In conclusion, improved safety is a significant advantage of industrial machinery fitting. Skilled fitters play a vital role in correctly installing machinery and ensuring proper fittings, reducing the risk of accidents on the factory floor. By investing in skilled professionals and prioritizing safety during installation and maintenance processes, businesses can create a secure working environment that fosters productivity and protects their most valuable asset—their employees.
Improved Product Quality – By ensuring that all parts are properly fitted and working correctly, businesses can ensure that their products meet high standards of quality and consistency.
Improved Product Quality: The Benefit of Industrial Machinery Fitting
In the competitive landscape of manufacturing, businesses strive to deliver products of the highest quality to satisfy customer demands and maintain a strong reputation. One significant advantage of industrial machinery fitting is its positive impact on product quality.
By ensuring that all parts are properly fitted and working correctly, businesses can guarantee that their products meet high standards of quality and consistency. Skilled fitters play a crucial role in this process by meticulously aligning components, calibrating sensors, and conducting thorough testing to ensure optimal functionality.
When machinery is installed correctly, it operates smoothly, minimizing the risk of errors or defects during production. Proper alignment and calibration prevent misalignments or inaccuracies that could affect product dimensions or performance. This attention to detail helps businesses maintain tight tolerances and produce items that meet precise specifications.
Consistency is another key aspect of improved product quality facilitated by industrial machinery fitting. When all parts are fitted correctly, machines operate consistently across production runs. This consistency ensures that each item manufactured meets the same high standards, reducing variations in product quality.
Moreover, fitters contribute to product quality by conducting regular maintenance and inspections. By identifying potential issues early on and addressing them promptly, they prevent malfunctions or breakdowns that could compromise product integrity. Preventive maintenance tasks such as lubrication or replacing worn-out parts also help maintain optimal machine performance over time.
The benefits of improved product quality extend beyond customer satisfaction. High-quality products result in fewer returns or warranty claims, saving businesses time and money associated with rework or replacements. Moreover, consistent quality builds trust with customers who rely on reliable products for their own operations or end-use.
In conclusion, industrial machinery fitting plays a vital role in enhancing product quality within the manufacturing industry. Skilled fitters ensure proper installation, alignment, calibration, and ongoing maintenance of machinery to minimize errors and variations while maximizing consistency. By investing in professional fitting services, businesses can achieve higher product quality, leading to increased customer satisfaction, reduced costs, and a stronger competitive edge in the market.
Cost Savings – Industrial machinery fitting can help companies save money in the long run as they will not need to replace faulty equipment or pay for expensive repairs due to improper installation.
Cost Savings: The Financial Advantage of Industrial Machinery Fitting
In the fast-paced world of manufacturing, companies are constantly seeking ways to optimize their operations and reduce costs. One significant advantage of industrial machinery fitting is the potential for long-term cost savings. By ensuring proper installation, businesses can avoid the need for expensive equipment replacements or repairs caused by improper setup.
When industrial machinery is not correctly installed, it can lead to a range of issues that have financial implications. Faulty alignment, incorrect wiring, or improper calibration can result in reduced efficiency, increased energy consumption, and even premature wear and tear on components. These problems not only hinder productivity but also lead to higher maintenance and repair expenses.
By investing in skilled fitters who understand the intricacies of machinery installation, companies can avoid these costly pitfalls. Fitters meticulously follow manufacturer specifications and guidelines to ensure that every component is correctly positioned and connected. This attention to detail minimizes the risk of malfunctioning equipment due to installation errors.
Properly installed machinery operates at optimal efficiency levels, resulting in reduced energy consumption and improved productivity. This translates into tangible cost savings over time as businesses spend less on utility bills and achieve higher output with fewer resources. Additionally, well-installed machinery tends to have a longer lifespan, reducing the need for premature replacements.
Furthermore, by avoiding expensive repairs caused by improper installation, companies can allocate their financial resources more effectively. Repairs often require specialized expertise and replacement parts that come at a significant cost. By investing upfront in professional fitters who ensure proper installation from the start, businesses can mitigate these potential expenses down the line.
Cost savings through industrial machinery fitting extend beyond just avoiding immediate repair costs; they also contribute to overall operational efficiency. When equipment operates smoothly without frequent breakdowns or interruptions due to faulty installation, production schedules remain on track. This leads to increased output and customer satisfaction while minimizing costly delays or penalties for missed deadlines.
In conclusion, industrial machinery fitting offers companies a strong financial advantage through long-term cost savings. By investing in skilled fitters who ensure proper installation, businesses can avoid the need for expensive equipment replacements or repairs caused by improper setup. This not only reduces maintenance and repair expenses but also improves efficiency, extends equipment lifespan, and enhances overall operational productivity.
For companies looking to optimize their manufacturing processes and maximize financial returns, industrial machinery fitting should be considered an essential investment. By prioritizing professional installation, businesses can reap the rewards of improved efficiency, reduced costs, and a competitive edge in the industry.
High cost of installation and maintenance
High Cost of Installation and Maintenance: A Con of Industrial Machinery Fitting
Industrial machinery fitting undoubtedly plays a vital role in the manufacturing sector, ensuring efficient operations and maintaining safety standards. However, it is important to acknowledge that there are some challenges associated with this profession. One significant con is the high cost of installation and maintenance.
The installation process of industrial machinery involves meticulous planning, precise alignment, and skilled labor. This level of expertise often comes at a premium price. Businesses investing in new machinery must allocate a substantial budget for professional fitters to ensure proper installation. The complexity and size of the machinery can further escalate the costs involved.
Moreover, maintenance is an ongoing expense that cannot be overlooked. Regular inspections, preventive maintenance tasks, and prompt repairs are crucial to keep machinery functioning optimally. Skilled fitters are required to conduct these activities, which can add up to significant costs over time.
The high cost of installation and maintenance can pose financial challenges for businesses, particularly small or medium-sized enterprises with limited budgets. It may require careful financial planning and prioritization to accommodate these expenses within their operational costs.
However, it is essential to recognize that while the initial investment and ongoing maintenance costs may appear high, they are necessary for long-term efficiency and safety. Neglecting proper installation or delaying necessary maintenance can lead to more significant issues down the line, such as frequent breakdowns, decreased productivity, or even workplace accidents.
To mitigate the impact of high costs associated with industrial machinery fitting, businesses can explore alternative options such as leasing equipment or outsourcing maintenance services. Leasing allows businesses to access advanced machinery without bearing the full upfront cost of purchase and installation. Outsourcing maintenance services to specialized firms can also provide cost-effective solutions by leveraging their expertise and economies of scale.
Additionally, proactive planning and scheduling regular maintenance activities can help prevent unexpected breakdowns or costly repairs in the future. By implementing preventive measures guided by fitters’ recommendations, businesses can minimize the risk of major machinery failures and mitigate potential financial burdens.
In conclusion, the high cost of installation and maintenance is a notable con associated with industrial machinery fitting. While it may present financial challenges for businesses, it is crucial to view these expenses as necessary investments in efficiency and safety. By carefully managing costs, exploring alternative options, and prioritizing preventive maintenance, businesses can strike a balance between ensuring smooth operations and maintaining their financial stability.
Risk of injury due to improper handling
Risk of Injury Due to Improper Handling: A Con of Industrial Machinery Fitting
While industrial machinery fitting is a crucial aspect of the manufacturing industry, it is not without its downsides. One significant con that cannot be overlooked is the risk of injury due to improper handling. The nature of this work involves dealing with heavy machinery, complex components, and potentially hazardous materials, making safety precautions paramount.
Improper handling of machinery during installation, maintenance, or repair can lead to severe injuries. Fitters who lack proper training or fail to follow safety protocols may inadvertently put themselves and others at risk. Mishandling heavy equipment can result in strains, sprains, or even more serious musculoskeletal injuries. Additionally, electrical hazards pose a significant threat if fitters are not adequately trained to handle live circuits or fail to follow proper lockout/tagout procedures.
Another aspect contributing to the risk of injury is inadequate personal protective equipment (PPE). Fitters must wear appropriate gear such as gloves, goggles, helmets, and steel-toed boots to protect themselves from potential hazards. Failure to use or maintain PPE correctly can result in injuries caused by falling objects, exposure to harmful substances, or accidents involving moving parts.
Furthermore, fatigue and lack of concentration can also contribute to the risk of injury during industrial machinery fitting. This type of work often requires long hours and intense focus. When fitters are fatigued or distracted, they may be more prone to making mistakes that could lead to accidents.
To mitigate the risk of injury due to improper handling during industrial machinery fitting, businesses must prioritize worker safety. Providing comprehensive training programs that cover proper handling techniques and safety protocols is essential. Regular refresher courses on safe practices and updates on industry standards should also be provided.
Employers should ensure that all necessary personal protective equipment is readily available and regularly inspected for damage or wear. Encouraging a culture of safety where employees feel comfortable reporting any safety concerns or near-miss incidents can also help identify potential hazards and prevent future accidents.
Fitters themselves must take responsibility for their own safety by adhering to established safety guidelines, using appropriate PPE, and seeking additional training when needed. They should be proactive in reporting any potential hazards they encounter in the workplace and actively participate in safety initiatives.
In conclusion, while industrial machinery fitting is essential for the smooth operation of manufacturing processes, the risk of injury due to improper handling is a valid concern. By prioritizing worker safety through comprehensive training, proper use of personal protective equipment, and fostering a culture of safety, businesses can minimize the likelihood of accidents and ensure the well-being of their fitters. Ultimately, a safe working environment benefits both employees and employers by reducing injuries, improving productivity, and enhancing overall job satisfaction.
Noise pollution from machinery operation
Noise Pollution from Machinery Operation: A Concern in Industrial Machinery Fitting
In the world of industrial machinery fitting, one significant concern that cannot be overlooked is noise pollution resulting from machinery operation. While the installation, maintenance, and repair of machinery are essential for smooth operations, the excessive noise generated can have detrimental effects on both workers and the surrounding environment.
The operation of heavy machinery often produces high levels of noise, which can lead to various health issues for those exposed to it over prolonged periods. Workers who are constantly exposed to loud noise levels may suffer from hearing loss or other auditory problems. Additionally, prolonged exposure to noise pollution can cause stress, fatigue, and even impact overall well-being.
Noise pollution not only affects the workers directly involved in machinery fitting but also has repercussions for those working in adjacent areas. The constant presence of loud noises can disrupt concentration levels, communication between workers, and overall productivity. It may also hinder effective communication during critical situations or emergencies.
Moreover, excessive noise can extend beyond the confines of a manufacturing facility and impact nearby residential areas or businesses. This can lead to complaints from local communities and potential legal issues if noise regulations are not adhered to. Therefore, it becomes crucial for businesses involved in industrial machinery fitting to address this con effectively.
To mitigate the negative impacts of noise pollution from machinery operation, several measures can be implemented. Firstly, investing in quieter machinery or upgrading existing equipment with noise-reducing features can significantly reduce overall noise levels. Additionally, implementing soundproofing measures within the facility itself can help contain and minimize the spread of noise.
Furthermore, providing workers with appropriate personal protective equipment (PPE) such as earplugs or earmuffs is essential in safeguarding their hearing health. Regular monitoring of noise levels within the workplace is also crucial to identify areas where improvements are required and take necessary actions accordingly.
In conclusion, while industrial machinery fitting is necessary for efficient manufacturing processes, it is important to acknowledge the con of noise pollution resulting from machinery operation. By implementing effective measures to reduce noise levels and protect the well-being of workers, businesses can create a safer and more comfortable working environment. Addressing this concern not only benefits the workers directly involved but also contributes to a harmonious relationship with surrounding communities.
Limited access to parts and components
Limited access to parts and components: A Challenge in Industrial Machinery Fitting
Industrial machinery fitting is a complex and demanding profession that requires skilled professionals to install, maintain, and repair machinery in manufacturing environments. However, one significant challenge that fitters often face is the limited access to parts and components.
In the fast-paced world of manufacturing, technology advances rapidly, leading to frequent updates and changes in machinery designs. As a result, finding the exact replacement parts for older or specialized machines can be challenging. Fitters may encounter difficulties in sourcing specific components that are no longer readily available on the market.
This limited access to parts and components can pose several challenges for fitters. Firstly, it can lead to extended downtime when a machine breaks down or requires repairs. Without immediate access to the necessary parts, fitters may struggle to restore operations promptly, impacting productivity and potentially causing financial losses for businesses.
Additionally, limited access to parts can also affect the quality of repairs or maintenance performed by fitters. In some cases, they may need to resort to alternative solutions or makeshift fixes due to unavailability of original components. While these temporary measures may keep the machinery running temporarily, they may not provide a long-term solution or guarantee optimal performance.
Moreover, with limited access to parts and components, fitters may face increased pressure to extend the lifespan of existing machinery beyond its intended use. This practice can compromise safety standards as well as overall efficiency. It becomes crucial for businesses and fitters alike to strike a balance between cost-saving measures and ensuring that equipment remains reliable and safe for operation.
To mitigate this challenge, collaboration between manufacturers, suppliers, and fitters is essential. Manufacturers should strive to provide comprehensive support by ensuring an adequate supply of spare parts for their machines over an extended period. This includes maintaining an inventory of critical components or offering suitable alternatives when original parts are no longer available.
Fitters can also play a proactive role by establishing strong relationships with suppliers and manufacturers. By staying informed about upcoming changes in machinery designs or advancements, they can anticipate potential issues and plan accordingly. Building a network of trusted suppliers who specialize in hard-to-find components can also prove beneficial in overcoming the challenge of limited access to parts.
In conclusion, limited access to parts and components is a significant con that industrial machinery fitters face. It can result in downtime, compromise the quality of repairs, and pose safety risks. However, by fostering collaboration between manufacturers, suppliers, and fitters, businesses can work towards finding viable solutions to ensure a smoother workflow, minimize disruptions, and maintain the efficiency and safety of their industrial machinery.
Potential environmental hazards from emissions
Potential Environmental Hazards from Emissions: A Con of Industrial Machinery Fitting
While industrial machinery fitting is an essential aspect of the manufacturing industry, it is important to acknowledge that it also presents certain challenges and drawbacks. One significant concern is the potential environmental hazards that can arise from emissions produced by industrial machinery.
Industrial machinery often relies on various fuels, such as diesel, natural gas, or coal, to power their operations. During the combustion process, these fuels can release harmful emissions into the atmosphere. These emissions may include pollutants such as carbon dioxide (CO2), nitrogen oxides (NOx), sulfur oxides (SOx), particulate matter (PM), and volatile organic compounds (VOCs).
The release of these pollutants can have detrimental effects on both human health and the environment. For instance, high levels of carbon dioxide contribute to climate change by trapping heat in the Earth’s atmosphere. Nitrogen oxides and sulfur oxides can contribute to air pollution and acid rain, which negatively impact ecosystems and human respiratory health.
Particulate matter emitted from industrial machinery can pose a significant risk to air quality. These tiny particles can be inhaled and cause respiratory problems or exacerbate existing conditions such as asthma or bronchitis. Additionally, volatile organic compounds released into the air can contribute to smog formation and have adverse effects on air quality.
Addressing these environmental hazards requires a multi-faceted approach. Firstly, businesses must prioritize investing in modern machinery that incorporates advanced technologies for emission control. This includes using low-emission fuels, implementing efficient combustion processes, and installing effective exhaust treatment systems.
Furthermore, regular maintenance and monitoring are crucial to ensure machinery operates optimally with minimal emissions. Routine inspections help identify any malfunctions or inefficiencies that may lead to increased pollution levels. By promptly addressing these issues through repairs or adjustments, businesses can mitigate potential environmental risks.
Government regulations also play a vital role in mitigating environmental hazards. Authorities enforce emission standards and set limits on pollutant levels, encouraging businesses to adopt cleaner technologies and practices. Compliance with these regulations is essential to minimize the impact of industrial machinery fitting on the environment.
In conclusion, while industrial machinery fitting offers numerous benefits to the manufacturing industry, it is important to recognize and address the potential environmental hazards associated with emissions. By investing in emission control technologies, prioritizing regular maintenance, and adhering to government regulations, businesses can mitigate these risks and work towards a more sustainable future. Striking a balance between industrial productivity and environmental responsibility is crucial for ensuring a healthier planet for future generations.