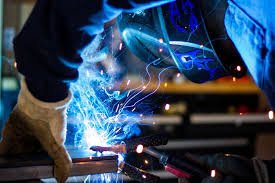
Mastering the Art of Welding and Fabrication: A Comprehensive Guide
The Art of Welding and Fabrication
Welding and fabrication are two essential processes in the world of metalwork. They play a crucial role in creating structures, machinery, and products that we use in our daily lives. Let’s delve into the fascinating world of welding and fabrication.
Welding
Welding is the process of joining two or more pieces of metal together using heat and pressure. It requires precision, skill, and expertise to create strong and durable bonds between metals. There are various welding techniques, including MIG (Metal Inert Gas), TIG (Tungsten Inert Gas), and Arc welding, each suited for different types of metals and applications.
Fabrication
Fabrication involves shaping raw materials into finished products through cutting, bending, and assembling processes. Skilled fabricators use a combination of tools such as saws, drills, presses, and welders to transform metal sheets or bars into functional components or structures.
The Importance of Welding and Fabrication
Welding and fabrication are essential in industries such as construction, automotive, aerospace, and manufacturing. Skilled welders and fabricators play a vital role in creating everything from skyscrapers to intricate machinery with precision and accuracy.
The Future of Welding Technology
Advancements in technology have revolutionised the welding industry. From robotic welding systems that improve efficiency to innovative materials that enhance durability, the future of welding looks promising. As new techniques emerge, welders must adapt to stay at the forefront of their craft.
In Conclusion
Welding and fabrication are not just technical skills; they are art forms that require creativity, precision, and dedication. The next time you see a towering skyscraper or a sleek automobile, remember that behind its creation lies the craftsmanship of skilled welders and fabricators.
Essential FAQs About Welding and Fabrication: Techniques, Careers, and Industry Insights
- What is welding and fabrication?
- What are the different types of welding techniques?
- How important is welding and fabrication in various industries?
- What skills are required to become a welder or fabricator?
- What safety precautions should be taken during welding and fabrication processes?
- How does technology influence the field of welding and fabrication?
- What are the common challenges faced by welders and fabricators?
- How can one pursue a career in welding and fabrication?
- What are the environmental impacts of welding and fabrication processes?
What is welding and fabrication?
Welding and fabrication are fundamental processes in the realm of metalwork. Welding involves joining two or more pieces of metal together using heat and pressure to create a strong bond. On the other hand, fabrication encompasses the shaping of raw materials into finished products through cutting, bending, and assembling techniques. In essence, welding is the act of bonding metals, while fabrication involves transforming these metals into functional components or structures. These processes are essential in various industries and require skilled professionals who possess expertise in handling metals with precision and care.
What are the different types of welding techniques?
One frequently asked question in the realm of welding and fabrication is, “What are the different types of welding techniques?” Welding encompasses a variety of methods, each tailored to specific materials and applications. Common welding techniques include MIG (Metal Inert Gas), TIG (Tungsten Inert Gas), Arc welding, and more. Each technique has its unique advantages and challenges, making it crucial for welders to choose the most suitable method based on the project requirements. By understanding the intricacies of different welding techniques, professionals in the field can effectively create strong and durable bonds between metals, ensuring the success of their fabrication projects.
How important is welding and fabrication in various industries?
Welding and fabrication play a critical role in various industries, serving as the backbone of construction, manufacturing, automotive, and aerospace sectors, among others. The importance of welding and fabrication lies in their ability to create strong and reliable structures, machinery, and products that are essential for everyday life. Skilled welders and fabricators are indispensable in ensuring the quality, durability, and safety of the end products used across different industries. Their expertise is vital in shaping the modern world we live in today.
What skills are required to become a welder or fabricator?
To become a successful welder or fabricator, a range of skills is essential. Firstly, proficiency in various welding techniques such as MIG, TIG, and Arc welding is crucial. Attention to detail and precision are also key attributes, as welders and fabricators must work with accuracy to create strong and durable metal structures. Problem-solving skills are valuable in troubleshooting issues that may arise during the welding process. Additionally, physical strength and dexterity are important for handling heavy materials and operating machinery safely. Continuous learning and adaptability to new technologies and materials are also vital for staying current in the ever-evolving field of welding and fabrication.
What safety precautions should be taken during welding and fabrication processes?
Safety is paramount in welding and fabrication processes to prevent accidents and ensure the well-being of workers. It is essential to follow strict safety precautions, such as wearing appropriate personal protective equipment (PPE) like welding helmets, gloves, and safety goggles to protect against heat, sparks, and UV radiation. Adequate ventilation in the workspace is crucial to prevent exposure to harmful fumes and gases produced during welding. Additionally, maintaining a clean and clutter-free work environment reduces the risk of tripping hazards. Regular equipment maintenance and proper training on safe welding techniques are also key aspects of ensuring a secure working environment for all involved in welding and fabrication processes.
How does technology influence the field of welding and fabrication?
Technology has significantly impacted the field of welding and fabrication, revolutionising traditional practices and enhancing efficiency and precision. The introduction of robotic welding systems has automated repetitive tasks, increasing productivity and reducing human error. Advanced welding techniques, such as laser welding and friction stir welding, have improved the quality and strength of welds, allowing for the joining of dissimilar materials with greater precision. Additionally, digital tools like computer-aided design (CAD) software enable fabricators to create intricate designs and prototypes with ease, streamlining the production process. Overall, technology continues to shape the future of welding and fabrication by pushing boundaries and introducing innovative solutions to meet industry demands.
What are the common challenges faced by welders and fabricators?
Welders and fabricators often encounter a range of challenges in their work. One common issue is achieving precise welds and accurate measurements, requiring a high level of skill and attention to detail. Another challenge is working with a variety of metals, each with its own properties and welding requirements. Additionally, ensuring the structural integrity and quality of the final product while meeting tight deadlines can be demanding. Safety concerns, such as exposure to fumes and hazards associated with hot metalwork, also pose significant challenges that welders and fabricators must navigate carefully. Overall, overcoming these obstacles requires expertise, experience, and a commitment to continuous improvement in the field of welding and fabrication.
How can one pursue a career in welding and fabrication?
To pursue a career in welding and fabrication, individuals can start by obtaining the necessary education and training. Many vocational schools and technical colleges offer welding programs that cover essential skills and techniques. It is also beneficial to gain hands-on experience through apprenticeships or internships with experienced welders and fabricators. Building a strong foundation in welding processes, safety protocols, and metalworking fundamentals is crucial for success in this field. Additionally, obtaining relevant certifications, such as those from recognised organisations like the Welding Institute (TWI) or the American Welding Society (AWS), can enhance one’s credibility and employability as a professional welder or fabricator.
What are the environmental impacts of welding and fabrication processes?
The environmental impacts of welding and fabrication processes are a significant concern in today’s industrial landscape. These processes often involve the use of high heat, electricity, and consumables such as gases and chemicals, which can contribute to air and water pollution if not managed properly. Emissions from welding fumes and gases can harm air quality, while improper disposal of waste materials can contaminate soil and water sources. It is crucial for welders and fabricators to adopt sustainable practices, such as using eco-friendly materials, implementing proper ventilation systems, and recycling waste products, to minimise their environmental footprint and contribute to a cleaner and healthier planet.