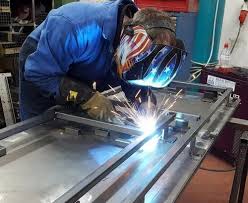
Mastering the Art of Welding Fabrication: Techniques and Innovations
The Art of Welding Fabrication
Welding fabrication is a skilled trade that involves the creation of metal structures by fusing various metal components together. It is a crucial process in industries such as construction, automotive, aerospace, and manufacturing.
Welding fabrication requires precision, expertise, and attention to detail. Welders use different techniques such as arc welding, MIG welding, TIG welding, and oxy-acetylene welding to join metals together. Each method has its own advantages and is chosen based on the specific requirements of the project.
One of the key benefits of welding fabrication is its versatility. Welders can create a wide range of structures and products, from simple frameworks to complex machinery parts. The durability and strength of welded structures make them ideal for applications that require robustness and reliability.
Quality control is essential in welding fabrication to ensure that the finished product meets industry standards for safety and performance. Skilled welders undergo rigorous training to master their craft and understand the intricacies of different metals and welding techniques.
As technology advances, so does welding fabrication. Innovations such as robotic welding systems have revolutionised the industry by increasing efficiency, accuracy, and productivity. These automated systems can perform intricate welds with precision, reducing human error and improving overall quality.
In conclusion, welding fabrication is a vital component of modern manufacturing processes. Skilled welders play a crucial role in creating durable and reliable metal structures that form the backbone of various industries. With continuous advancements in technology and techniques, the art of welding fabrication continues to evolve and adapt to meet the ever-changing demands of the industrial landscape.
Essential Tips for Safe and Effective Welding Fabrication
- Always wear appropriate safety gear, such as welding helmet, gloves, and protective clothing.
- Ensure proper ventilation in the welding area to avoid inhaling harmful fumes and gases.
- Clean the surfaces to be welded thoroughly to ensure strong and clean welds.
- Use the correct welding technique based on the type of metal being welded (e.g. MIG or TIG welding).
- Check your equipment regularly for any signs of damage or malfunction before starting work.
- Practice good weld bead control to create strong and consistent welds.
- Inspect your welds after completing them to ensure they meet quality standards.
Always wear appropriate safety gear, such as welding helmet, gloves, and protective clothing.
It is essential to prioritise safety when engaging in welding fabrication tasks. Always wear the necessary safety gear, including a welding helmet, gloves, and protective clothing, to safeguard yourself from potential hazards. The welding helmet protects your eyes and face from intense light and sparks, while gloves shield your hands from burns and cuts. Additionally, wearing appropriate protective clothing helps prevent exposure to heat, flames, and flying debris. By consistently adhering to these safety precautions, welders can ensure a secure working environment and minimise the risk of injuries during welding fabrication processes.
Ensure proper ventilation in the welding area to avoid inhaling harmful fumes and gases.
Proper ventilation is crucial in the welding area to prevent the inhalation of harmful fumes and gases. Adequate airflow helps to disperse these potentially hazardous substances, reducing the risk of respiratory issues for welders. By ensuring a well-ventilated workspace, workers can protect their health and safety while maintaining a productive and comfortable environment for welding fabrication tasks.
Clean the surfaces to be welded thoroughly to ensure strong and clean welds.
To achieve strong and clean welds in welding fabrication, it is crucial to thoroughly clean the surfaces to be welded. Removing any dirt, rust, oil, or contaminants from the metal surfaces ensures proper fusion and bonding during the welding process. Clean surfaces promote better adhesion and prevent defects in the weld, resulting in a high-quality and durable finished product. By taking the time to prepare and clean the surfaces meticulously, welders can ensure that their welds are strong, reliable, and meet industry standards for safety and performance.
Use the correct welding technique based on the type of metal being welded (e.g. MIG or TIG welding).
When engaging in welding fabrication, it is crucial to use the correct welding technique that aligns with the type of metal being welded. Whether it is MIG or TIG welding, selecting the appropriate method based on the specific characteristics of the metal ensures a strong and durable bond. Different metals have varying properties that require tailored approaches to achieve optimal results. By understanding and applying the right welding technique, welders can enhance the quality and integrity of their work, ultimately contributing to the success of the fabrication project.
Check your equipment regularly for any signs of damage or malfunction before starting work.
Before beginning any welding fabrication work, it is crucial to check your equipment regularly for any signs of damage or malfunction. By conducting a thorough inspection of your welding tools and machinery, you can identify potential issues early on and prevent accidents or errors during the welding process. Ensuring that your equipment is in good working condition not only promotes safety in the workplace but also helps maintain the quality and integrity of the welds produced. Remember, a proactive approach to equipment maintenance is key to successful welding fabrication projects.
Practice good weld bead control to create strong and consistent welds.
To achieve strong and consistent welds in welding fabrication, it is essential to practice good weld bead control. By mastering the technique of controlling the weld bead, welders can ensure that the molten metal is deposited evenly and smoothly, resulting in a sturdy and uniform weld. Proper bead control not only enhances the structural integrity of the welded joint but also contributes to the overall quality and appearance of the final product. Consistent practice and attention to detail in weld bead control are key factors in producing high-quality welds that meet industry standards for strength and durability.
Inspect your welds after completing them to ensure they meet quality standards.
After completing a welding fabrication project, it is essential to inspect your welds thoroughly to ensure they meet the required quality standards. By conducting a careful inspection, you can identify any potential defects or imperfections that may compromise the integrity of the weld. This step is crucial in maintaining the structural integrity and safety of the finished product. Regular inspection of welds not only ensures compliance with industry standards but also guarantees the longevity and reliability of the welded structure. Remember, quality inspection is a fundamental aspect of welding fabrication that should never be overlooked.